Sound is an important part of the consumer experience for many products – think of the satisfying clunk of a well-built car door – but it is often a subconcsious experience that engineers and product designers don’t properly consider until a problem occurs.
Whether a product’s sound is a core part of its functionality (think of a small but mighty pair of bluetooth speakers) or a side effect of its use (such as the wind whistling across your car’s sunroof), in modern product development it is becoming increasingly important to be able to accurately predict the acoustic qualities of your designs before they’re manufactured.
Perhaps you’ve run a simulation in Ansys Mechanical, Ansys Fluent, Ansys LS-DYNA or Ansys Motion, but did you know you can now render the predicted sound sources so that you can actually listen to and further analyse the predicted sound generated by your product?
Ansys VRXPERIENCE Sound allows acoustics engineers to create immersive 3D soundscapes based on site recordings, CAE simulation outputs or a virtual reality (VR) environment. Typically, engineers use VRXPERIENCE Sound to perform tasks such as:
• Analysing sound quality
• Setup of psychoacoustic tests based on a listener panel to obtain statistics about the real perception of your sounds.
• Creating high-precision reproductions of 3d sounds and original timbres in a predefined space.
• Producing audio for simulators and VR platforms – available for cars, aircraft and trains
• Setup of jury testing for sound perception to measure user preferences, positioning & unpleasantness
• Listening to outputs of mechanical and/or fluids simulations, and modify sounds to evaluate effects of level changes on components.
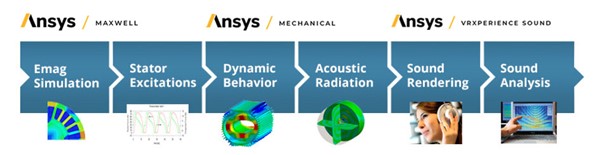
In order to listen to the outputs of your mechanical or fluids (or multiphysics) simulation, then you must first produce an accurate simulation result – so let’s revisit the most important considerations for any proposed acoustics simulation: what are we trying to achieve, what physics is relevant and what is the right computational approach?
Typically, engineers implement Ansys Acoustics tools to adopt a virtual testing approach which lowers production times and reduces the risk of cost overheads associated with re-engineering a product that doesn’t meet acoustic standards (when a problem is identified late in a product development cycle). Acoustics problems can often be classified as Flow-induced noise (Aero-acoustics) or Structure-induced noise (Vibro-acoustics), or a mix of both.
Flow induced noise deals with inherently unsteady flow fields and can involve internal or external flow noise sources. Specific modelling approaches are recommended to accurately model flow noise sources, including appropriate meshing, boundary conditions, solver techniques and solver methodology depending on the type of noise being generated, accuracy required and available hardware– these are all discussed in this Flow-Induced Noise webinar recording which includes industrial examples such as fan acoustics, blower acoustics, valve acoustics, high speed flows.
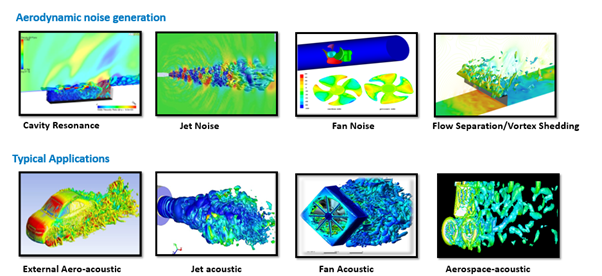
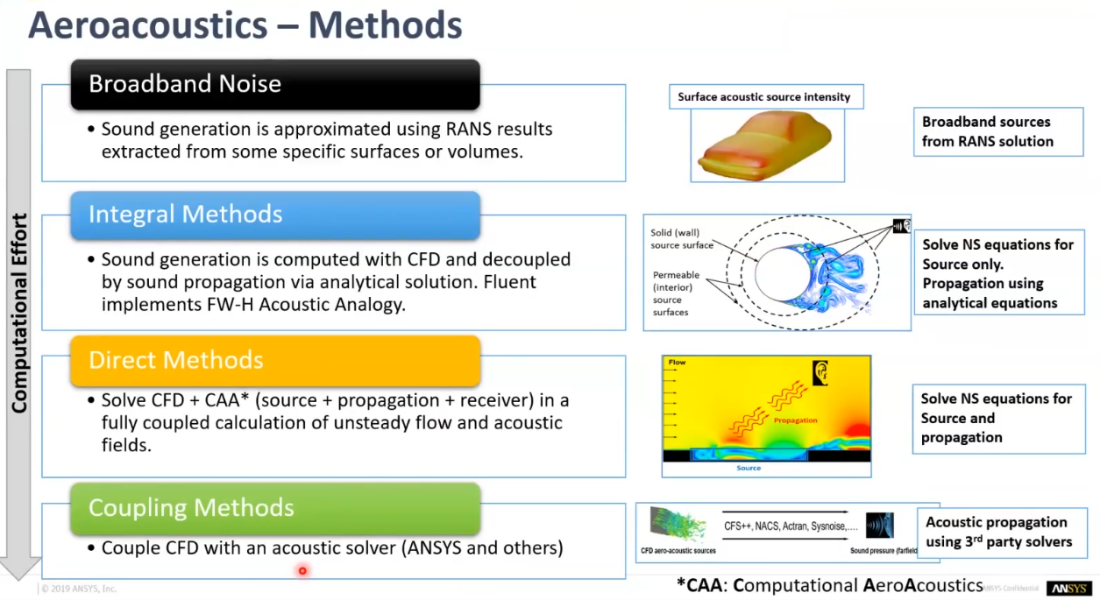
Prediction of sound propagation and structure-borne noise plays an important role in the design of many products. Examples include calculating transmission loss (TL) of a Silencer, noise caused by vibrating structural components, transmission of sound through thin panels.
Solving these types of acoustic wave propagation problems can be done either coupled (with fluid and structural domains solved simultaneously) or uncoupled (with the structural analysis performed first, followed by the acoustics analysis). The coupled approach is used when both structural vibrations and acoustic waves have a mutual influence: for example, when simulating a thin speaker cone whose deformations will be influenced by the pressure waves. Conversely, an uncoupled approach is valid when the acoustic waves do not affect the vibration of the structure, as is often the case for larger or stiffer parts.
To help determine whether a coupled or uncoupled approach is recommended for your application, this Structure-borne Noise webinar recording is a valuable resource which considers:
• Overview of FE formulation of Vibro-Acoustic Equations
• Material modelling
• Transfer admittance
• Vibro-Acoustics
• Random acoustic diffuse sound field analysis
• Visco-Thermal Acoustics
• Far Field Results Post Processing
Another important consideration remains if you’re dealing with large domains and/or high frequencies, is when to use a Boundary Element method approach (which is available in Ansys LS-DYNA). As we know, the frequency range for audible noise is broad – spanning from ~20 Hz – 20 kHz – and as the frequency range we want to simulate increases, so too does the model size (as the wavelength becomes smaller and smaller, we’ll need a much finer mesh to resolve the wavelength, which can significantly increase the mesh & model size).
Conventionally, at low frequency ranges up to ~1000 Hz, structures exhibit distinct mode shape or a distinct resonance frequency and a conventional FEA acoustic approach can be used. As we move to higher frequency ranges, it becomes more difficult to distinguish individual mode shapes (or natural frequencies occur very close together), and we require a very fine mesh in order to resolve these features.
At mid frequency ranges – the Boundary Element Method (BEM) can be used to provide a useful option which bridges the gap of applicability between FEA (max ~1000 Hz) to a Statistical energy approach (SEA) used at much higher frequencies (above ~2000 Hz can take average energy within frequency bands), as shown below:
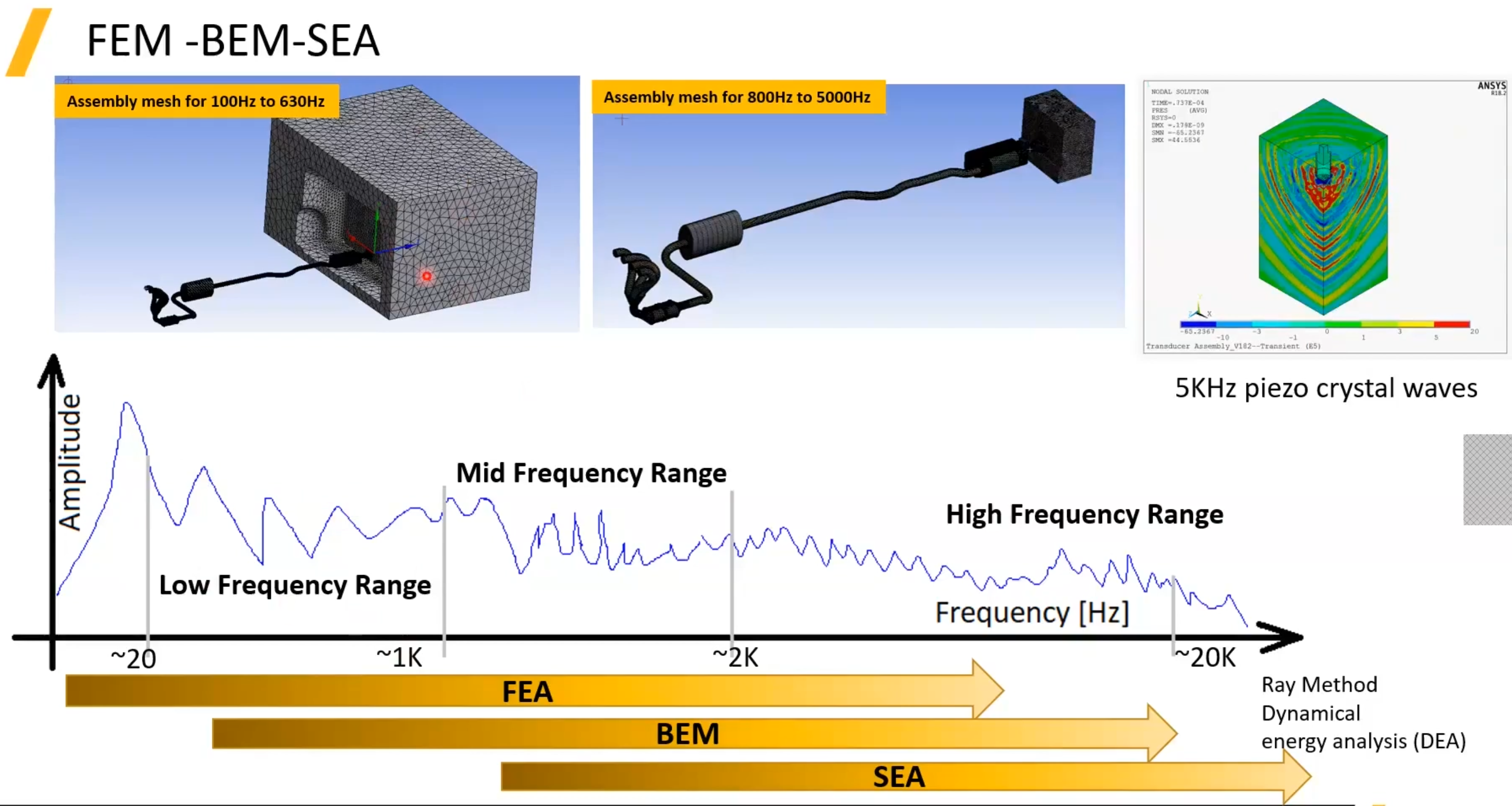
Ansys Electromagnetic tools can be combined with Ansys Mechanical to address noise from electrical machines that may be caused by fluctuating electromagnetic forces.
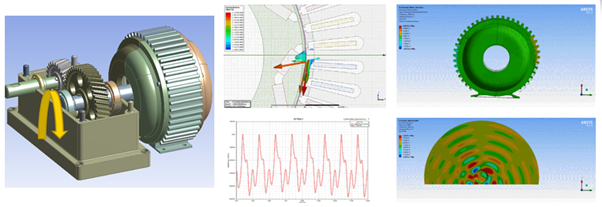
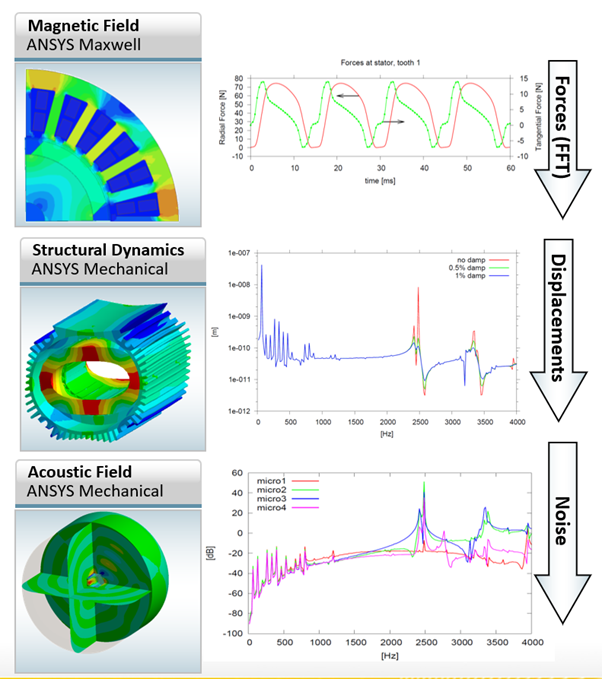
You may be *lucky* that the characteristics of your application will require simulation of a full multiphysics system to provide an accurate acoustics prediction. In this Multiphysics Acoustics webinar recording, the requirements and options to tackle multiphysics acoustics problems are discussed, including:
• Coupling between flow pressure (CFD) and vibro-acoustics (FEM)
• Coupling between electromagnetic forces and vibro-acoustics for electrical machine
• Coupling between MEMS and Acoustics for Sensor Application
• Transfer of loading data from time domain to frequency domain
• Application Example: Prediction of windshield noise
• Application Example: Prediction of electric motor noise
As one example of the complete workflow – starting with high-fidelity physics-based simulations (in this case, aeroacoustics using CFD) through to psychoacoustics analysis using VRX Sound – we recommend you watch the recording of this recent webinar from Frank Kelecy at Ansys who uses the example of drone propeller noise from a hovering quadcopter to demonstrate the entire workflow, covering:
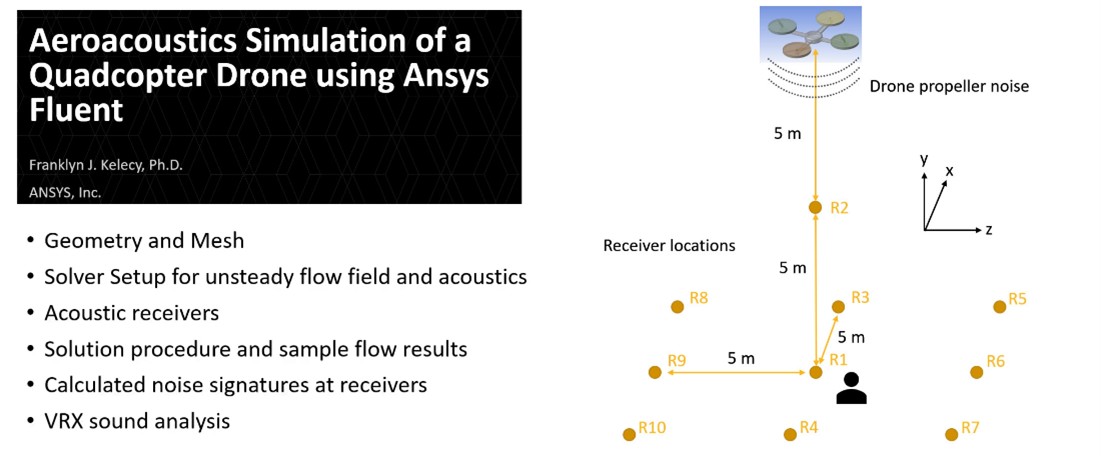
Acoustics simulation is not a straightforward topic, but the potential benefits are significant and certainly worth the investment in considering the available approaches and deciding which is the best method to simulate acoustics for your particular application. And remember that once you have reliable simulation results, you can leverage the full power of VRXPERIENCE Sound to analyse sound quality and perception and iterate to explore the impact of design changes.
If you would like to discuss the right approach for acoustics simulations in a specific project, contact LEAP to arrange a no-obligation chat by clicking here to speak with one of our simulation experts to help get started.