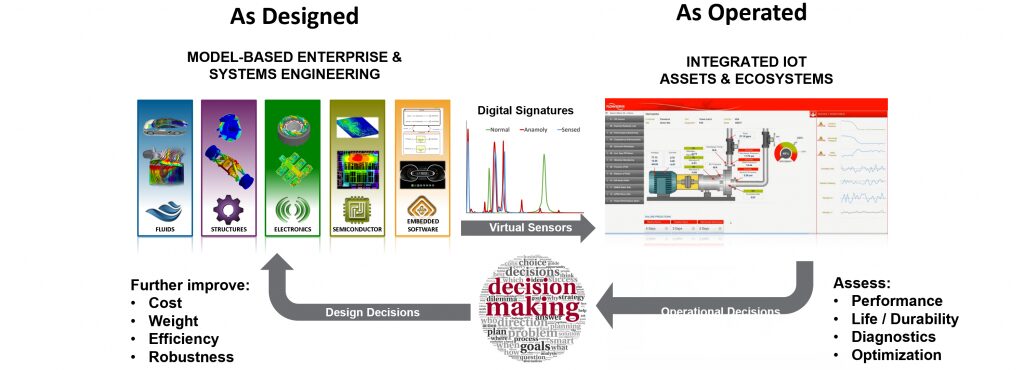
The hype around digital twins is justified, with clear potential to deliver numerous technical and revenue benefits to innovative organisations. A digital twin is enabled by the advent of cheap and reliable sensors communicating remotely (forming the Industrial Internet of Things), big data / machine learning alogorithms, plus the ability to construct a simulated virtual system representing the performance a product/process.
As with all engineering simulations, the scope of digital twins may vary depending on the specific technical or business requirements they are trying to address. As examples, digital twins may be developed to focus on:
– accelerating the next-generation of design and development by simulating specific components (with real-life boundary and operating conditions informed by the digital twin)
– or optimising an overall system, by identifying and troubleshooting system-level process issues by combining component performance with system-level interactions during real-life boundary/operating conditions.
What is the role of simulation in a digital twin?
Real-world products still only have a limited number of sensors, and some components cannot have adequate sensors placed within them due to cost or other constraints. A real-time virtual replica provides significant insight and value to an organisation – by combining known data with simulation to “fill in the gaps”, we have an unlimited number of “virtual sensors” provided by simulation. Components can undergo monitoring, diagnostics, and future predictions can be made – remotely operated using a digital twin.
So how does this work in practice?
Information about the asset is gathered through mounted sensors as well as through control system inputs. This information is leveraged through a variety of means: IIoT and data analytics provide useful information about current performance and trends. The inclusion of simulation allows us to make broader inferences about the asset with ever-increasing accuracy. These inferences can be about the current state of the asset, predictions about the future state, or help to understand operating conditions that are outside of the normal operating conditions.
Here at LEAP Australia we are fortunate to work with both ANSYS TwinBuilder and PTC Thingworx – and we have built multiple examples to demonstrate the workflow of constructing and operating a real-world digital twin. As well as providing the means to create the ROM, ANSYS TwinBuilder also provides the platform to include the ROM as part of a larger system of components. PTC’s Thingworx IoT platform provides the means through which the sensor data is collected, collated and communicated.
In the “How To” video you can see below, we explain how are operating a physical asset (a raspberry pi) which is representative of any real-world “smart connected product” – ie. a product or equipment fitted with sensors that communicates information about the current operating conditions i.e. in this case, we are sending IoT data on the amount of power that is being consumed and the speed at which the cooling fan is running. Our simulation tool (ANSYS CFD) helps us to gain valuable information about the thermal state of the asset for all conceivable operating conditions (as well as the inconceivable). ANSYS TwinBuilder (TB) then processes this data (some simulations may take many hours to generate all the design points) and produce a Reduced Order Model (ROM) that can be used by the digital twin to make near-instant predictions about the current state of the system, based on the input data provided (fan and power).
As well as coordinating the data flow between real-world IoT data and simulation-based ROMs, ANSYS TwinBuilder has a wealth of built-in tools designed to allow us to fully leverage the potential of the digital twin concept for our business needs:
Simulation-based ROMs
The ability to generate reduced order models is one of the major strengths of the TwinBuilder program. The reduced order model allows us to characterise otherwise intricate and convoluted systems into seemingly simple relationships between one or many inputs and outputs. This characterisation of the relationship between inputs and outputs can be applied to countless systems. ANSYS allows us to simulate the breadth of fluid, structural and electromagnetic systems, the digital twin is pervasive in its ability to represent any of these complex systems in instantaneous or real-time means.
Modelica library
The Modelica standard library contains over 1600 Modelica model components that can be used to represent a range of different physical systems. The open-source physical component-based libraries increase the number of use cases for the digital twin/system simulation landscape within TwinBuilder. This allows for more accurate real time modelling of complex 3D systems to be used to make a wider variety of predictions and analyses.
SCADE
Though TwinBuilder has its own ability to design and test control systems the inclusion of SCADE Suite significantly enhances these capabilities. SCADE has proven certified use cases many companies across the major engineering disciplines including aerospace, railway, energy and industrial.
We hope you’re excited by the potential of Digital Twins for your own company and can see the simplicity of using ANSYS TwinBuilder and PTC Thingworx to setup and operate a Digital Twin. LEAP’s engineers have already created these working examples that we can show you (this is not just a powerpoint presentation!) – contact your local LEAP office and arrange a time to touch and feel one of these real, operating digital twins and learn more about the value a digital twin can bring to your organisation.
I am interested in FEA with digital twin. is there relevant training course?
If you’re in Australia or New Zealand, please speak with your local LEAP office. Otherwise we recommend the courses offered by Ansys at https://courses.ansys.com/ as a good starting point. Good luck with your project!