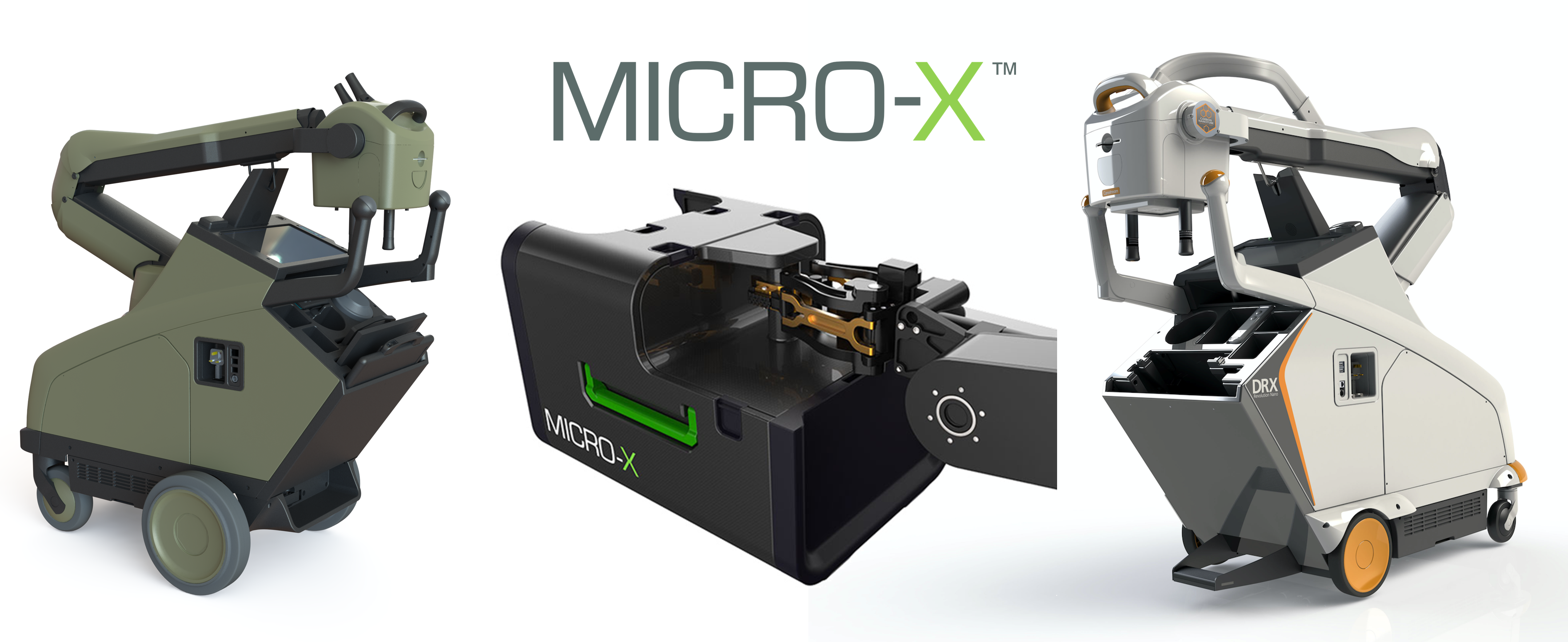
Guest blog by Caitlin Wouters, Mechanical Engineer (Biomedical), Micro-X
Micro-X is an Australian company that designs and manufactures mobile x-ray carts. Micro-X has developed innovative nanotube technology in order to develop a lightweight x-ray tube, aiding in the development of a mobile, wireless and lightweight x-ray cart. Due to the global COVID-19 pandemic there was a large increase in demand for our ‘Nano’ x-ray carts for diagnosis of the disease. This caused a very large increase in sales in the last quarter for carts. This was in particularly high demand in Asia and even here in Australia.
This increase in demand also showcased a need in the market for mobile x-ray carts for more robust applications such as military hospitals and emergency temporary hospitals where the conditions are less ideal. This has promoted an increased focus in the engineering team at Micro-X to make the newer model ‘Rover’ x-ray cart which is more suited to military and rough terrain mobile medical x-ray. In the light of the immediate need for this product, it was determined to be fast tracked to market. The use of simulation with ANSYS has made this effort significantly more streamlined.
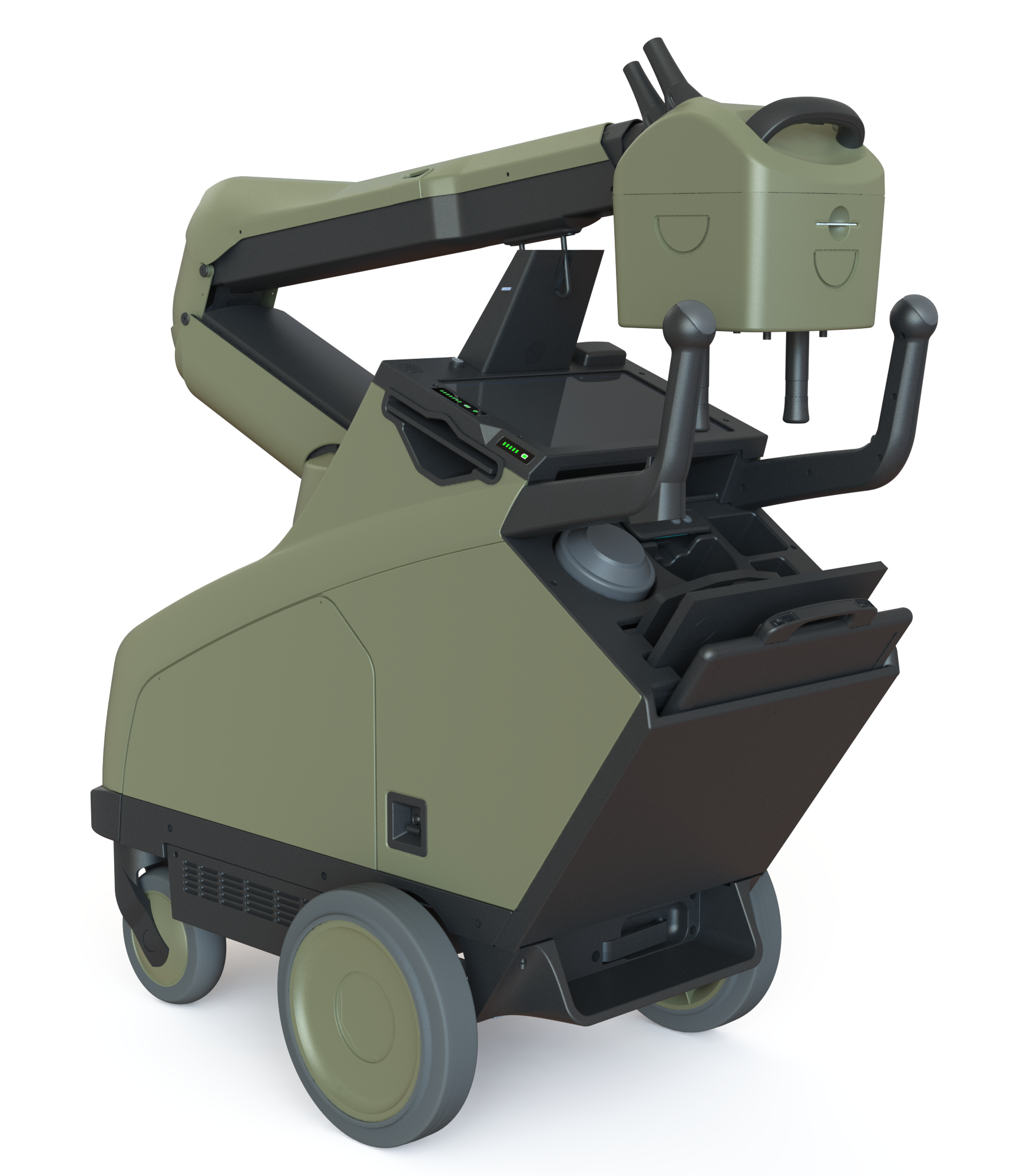
Figure 1: Rover x-ray cart
Ansys software has allowed modelling of mechanical changes to be done very swiftly so that Micro-X engineers could rapidly test multiple design changes and ideas. Structures can be modelled, and simulated loads and conditions applied to these varying geometries. This allows potential problems to be found early on before time and money is spent on producing physical prototypes for testing. With a more refined basis of prototype, this can reduce timings from multiple trials talking half to a third of the time and money. This also allows novel designs to be tested since there is less time or money attached to the testing.
One relevant example of this is in the analysis of the mechanical loads on the base for robust protection of internal components. By reviewing the stress in the part, Micro-X engineers can determine if the design has enough strength to undergo regular & repeated use, or engineers can review the predicted displacements to check for interference with critical adjacent parts.
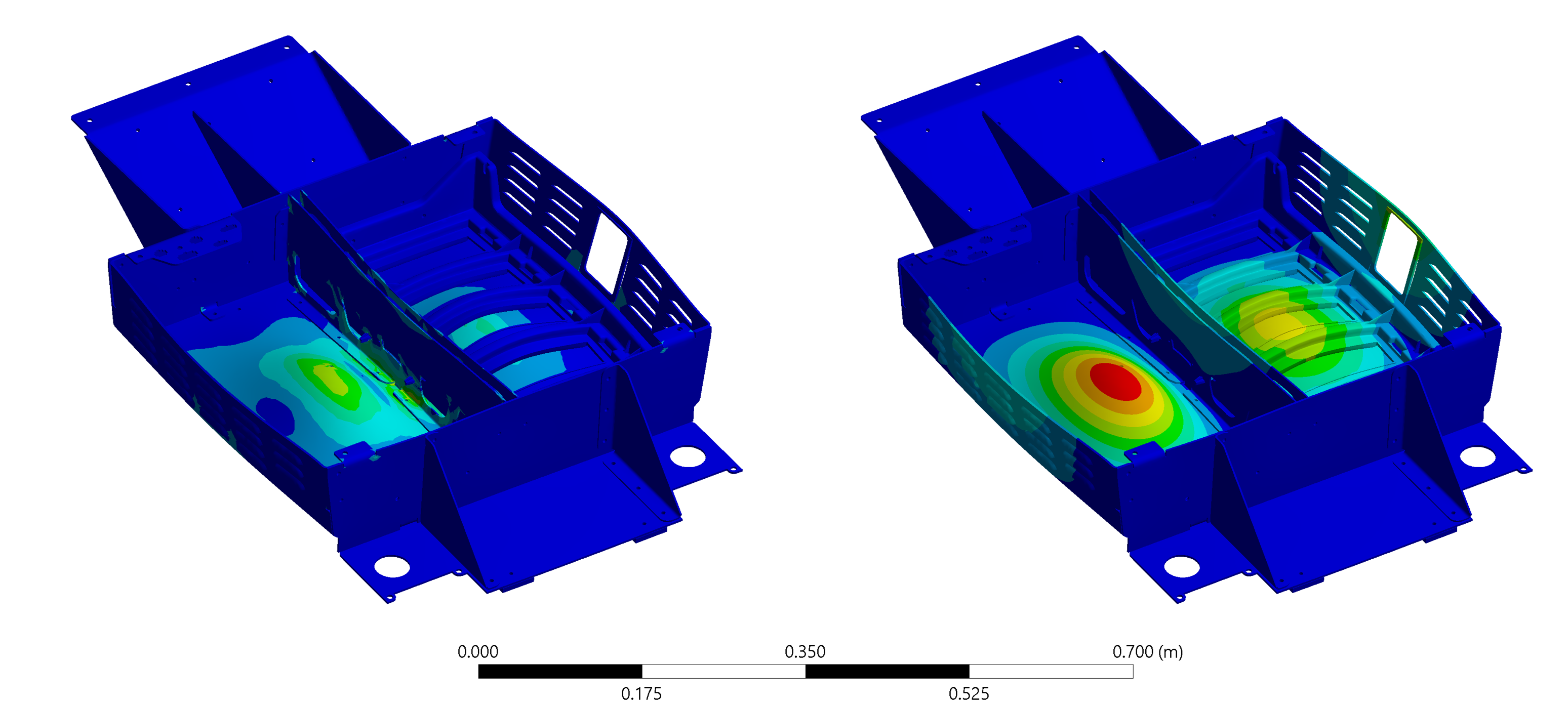
Figure 2: Stress and Deformation on battery box
Micro-X engineers have also modelled complex heat distribution on components from the tube internals to airflow around electrical components in order to ensure sensitive components do not overheat. A heat distribution through a part was reviewed in the simulation results which allows Micro-X engineers to review why a method of failure may be occurring, and adjust the design accordingly.
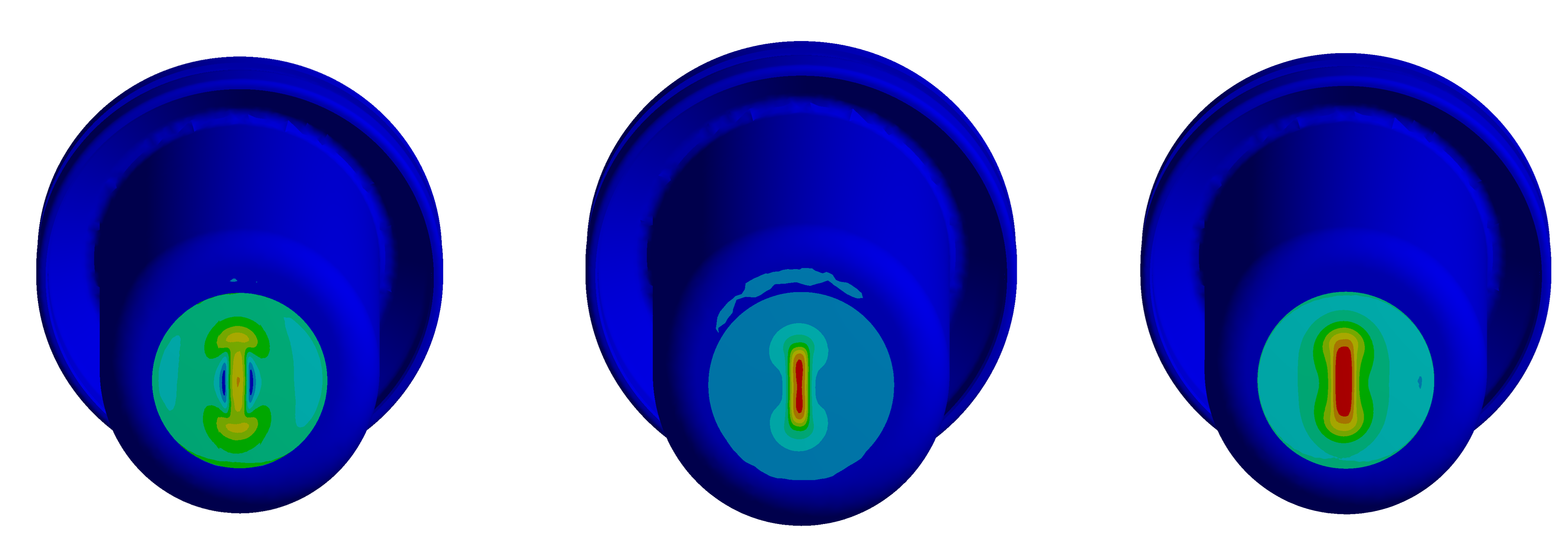
Figure 3: Comparison of Stress contours with variations in anode thickness
Ansys Mechanical simulations have allowed Micro-X to undertake complex analysis very quickly, greatly aiding in the swift development of our technology while still designing to the very reliable standards required for medical equipment. You can learn more about Micro-X and our products by visiting our website here.