[vc_row][vc_column][vc_column_text]It is well known that, compared to traditional materials, the fabrication of structures using composite materials offers clear benefits when designing high-performance products that require extreme strength and stiffness, combined with lower weight. However, the use of composite materials also presents additional challenges, as their mechanical properties are heavily influenced by loading direction and their brittle nature makes fracture a very serious possibility for poorly designed components.[/vc_column_text][/vc_column][/vc_row][vc_row][vc_column][vc_video link=”https://youtu.be/1JdP8AzSDW8″][/vc_column][/vc_row][vc_row][vc_column][vc_column_text]The ANSYS Composite PrepPost (ACP) suite has been specially designed to address these unique complexities of composite materials and aid engineers in designing high performance and safe components. This blog will follow the design and analysis of a composite wheel hub commonly used in high performance consumer and race cars.[/vc_column_text][/vc_column][/vc_row][vc_row][vc_column width=”1/2″][vc_single_image image=”1390″ img_size=”medium” alignment=”center” onclick=”link_image”][/vc_column][vc_column width=”1/2″][vc_single_image image=”1391″ img_size=”medium” alignment=”center” onclick=”link_image”][/vc_column][/vc_row][vc_row][vc_column][vc_column_text]The fabrication of composite structures is based on the layering of multiple plies of composite fabric onto a mould with the strong, stiff fibres orientated along key loading directions. Localised reinforcement with additional plies and correct ply angles are key to optimising the layup for maximum performance and minimum weight. This flexible fabrication process is also a key complexity of composite design; complex fabric shapes and multiple overlapping layers can become difficult to formulate but is easily managed with the pre-processing module of ACP. Individual fabric pieces are specified by geometry selection and can be treated separately in ACP with thickness and ply orientation.[/vc_column_text][/vc_column][/vc_row][vc_row][vc_column width=”1/2″][vc_column_text]
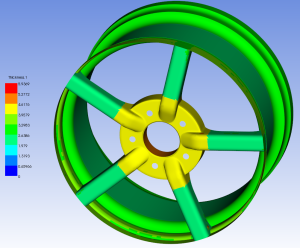
[/vc_column_text][/vc_column][vc_column width=”1/2″][vc_column_text]
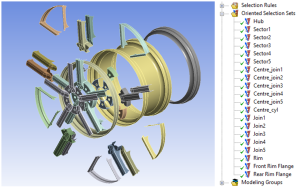
[/vc_column_text][/vc_column][/vc_row][vc_row][vc_column][vc_column_text]An added complexity of the composite manufacturing process is the issue of draping, it is the reorientation of a fabric when it is laid over a curved surface, the intended ply orientation is changed across the curve and its effect of fibre orientation can have a big impact on load carrying capability. Seen below, ANSYS ACP includes a draping algorithm which can be used to accurately account for the fibre rotation with fabric draping and updates the material orientation so that any change in mechanical properties will be accounted for in structural analysis.[/vc_column_text][/vc_column][/vc_row][vc_row][vc_column][vc_column_text][/vc_column_text][/vc_column][/vc_row][vc_row][vc_column][vc_column_text]With an accurate recreation of the composite layup completed in ACP (Pre) the model can be transferred to numerous ANSYS solvers for analysis. For thin shell components the composite layup can be consolidated into a single shell body for computational efficiency. Alternatively, the component can be automatically extruded into a solid or solid shell body allowing analysis of through thickness properties or delamination strength.[/vc_column_text][/vc_column][/vc_row][vc_row][vc_column][vc_column_text]
[/vc_column_text][/vc_column][/vc_row][vc_row][vc_column][vc_column_text]Complete integration of layup properties into ANSYS Mechanical allows ply by ply stress analysis and composite specific damage modelling from a multitude of industry proven failure criteria including Tsai-Wu, Hashin and Puck.[/vc_column_text][/vc_column][/vc_row][vc_row][vc_column][vc_column_text]
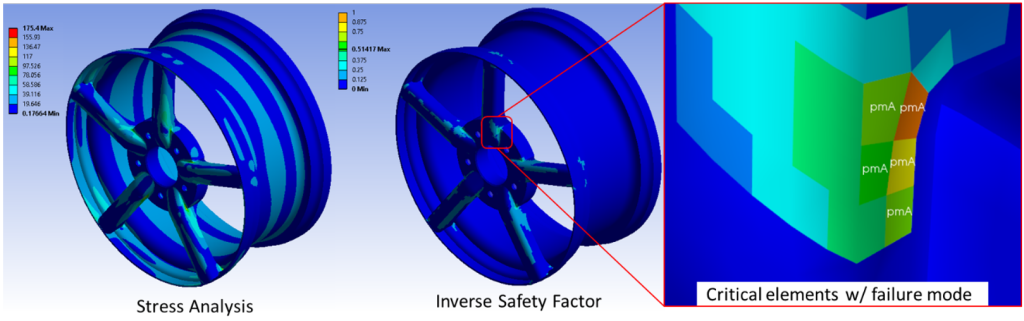
[/vc_column_text][/vc_column][/vc_row][vc_row][vc_column][vc_column_text]Damage tolerance of composite materials is also a key concern for industry. ANSYS has made the prediction of safety factors within ACP a very simple process, allowing engineers to detect the many distinct failure modes that can present in composite structures including matrix cracking, delamination and fibre breakage. Critically loaded locations within the design are also highlighted for reinforcement or adjustment of fibre orientation in further design iterations.
As with any simulation process, the full value is only realised using a design optimisation approach. As with other ANSYS products within the Workbench, complete parameterisation of the composite layup is possible within ACP – allowing you to control and parameterise the layup thickness, fibre orientation and reinforcement zones.[/vc_column_text][/vc_column][/vc_row][vc_row][vc_column][vc_column_text]
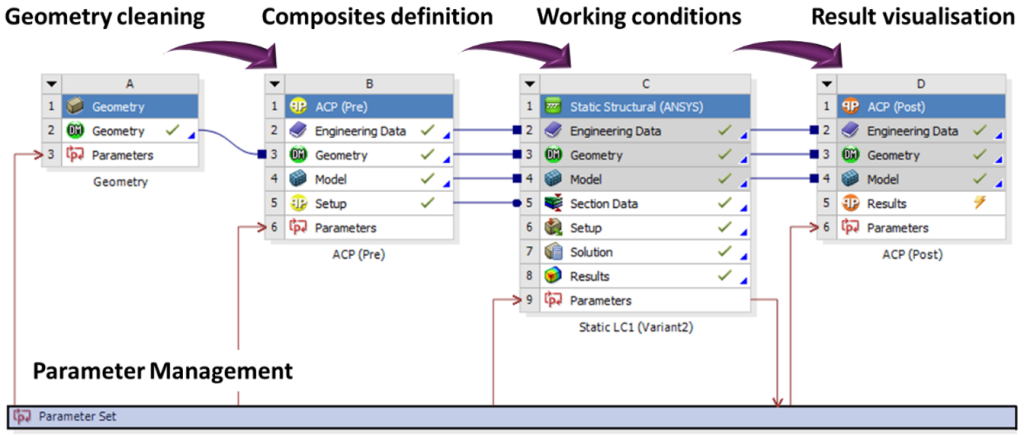
[/vc_column_text][/vc_column][/vc_row][vc_row][vc_column][vc_column_text]A parameterised layup, in conjunction with analysis outputs, can be used to generate an optimisation project within ANSYS DesignXplorer for ultimate tailoring of the component for the expected loading, leading to higher performance and minimum weight.[/vc_column_text][/vc_column][/vc_row][vc_row][vc_column][vc_column_text]
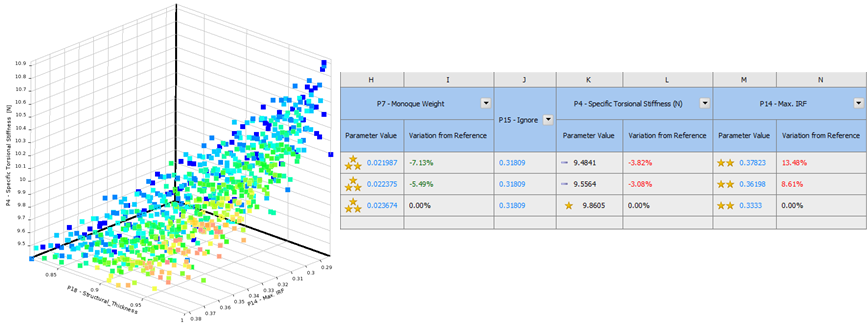
[/vc_column_text][/vc_column][/vc_row][vc_row][vc_column][vc_column_text]The ANSYS Composite PrepPost suite provides engineer the tools to tackle the added complexities of designing composite products. From pre-processing tools such as draping algorithms and complex fabric shape management to advanced failure analysis and integration to Multiphysics solvers, ANSYS Composite PrepPost allows engineers to produce higher performance and safer composite structures than ever before.[/vc_column_text][/vc_column][/vc_row]
Hi, would it possible for me to get a full video of the tutorial as it will beneficial for my project thanks.
Is it possible to study De-lamination Effects on ACP?
How can we achieve such smooth edges along the circular profile of the rim?? is there any design recommendations on lay-up process or in creating named selections for achieving smooth transitions along the circular edges?
Can i get full video link, that could be so helpful for my project
This is the best place to start: https://www.youtube.com/watch?v=f2Nik2-Qs0M