We sat down with Caecilia Potter, Founder & CEO, and Marko Trifunović, Senior Development Engineer, Venso Labs to talk about the VensoFlow process originally developed by Emeritus Professor Owen Potter AM, how insights from simulation are helping their team to continue to understand and further improving this process, and their recent company milestones for seed coating applications
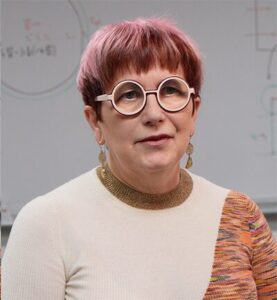
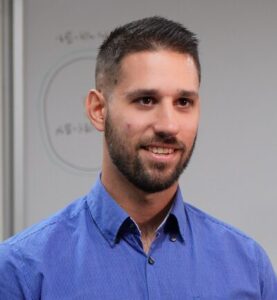
Some background on VensoLabs and the VensoFlow technology
Venso Labs technical founder was Emeritus Professor Owen Potter AM, an internationally renowned research chemical engineer, who developed a range of innovations in fluidisation to resolve difficult business challenges and improve sustainability.
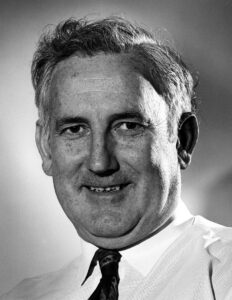
His cleaner, smarter particle processing invention, VensoFlow, is energy efficient, low CAPEX, proven up to 100x more even than competitive technologies. The superior process control benefits of VensoFlow will be unlocked using Ansys CFD Simulations and IIoT Process Control software (with PTC ThingWorx) to better predict and manage the temperature of particles and coatings.
The VensoFlow technology involves small particles (liquid or solid) being injected into a gas stream (either vertical or horizontal) allowing for a very high surface area exposed to the gas, facilitating efficient interaction of the particles with the gas for either mass or heat transfer or catalytic reactions with significantly lower pressure drop compared to existing methods such as fluidised beds and rotary drums.
Caecilia Potter is the commercial founder and is committed to using her father’s legacy, VensoFlow, to help engineers solve critical global problems sustainably. She led the team of engineers to build the pilot, prove the VensoFlow concept, lodge the second patent family and win a $946,000 AusIndustry EP grant for our first commercial application – agricultural seed coating and drying to offer unlimited liquid coatings in discrete layers and better preserve heat sensitive biological coatings which increase yields and reduce environmental pollution.
Caecilia explains “our 2021 solid-gas pilot proved up to 90% heat transfer effectiveness is readily achievable. We have also completed the first lab scale pilot of the liquid-gas module which offers very large surface area without the need for packing and may also mitigate the need for water washing waste gases for processes such as CO2 capture. The findings from this pilot will allow us to further develop our virtual model and run virtual pilots in preparation for building a full-scale vertical contactor.”
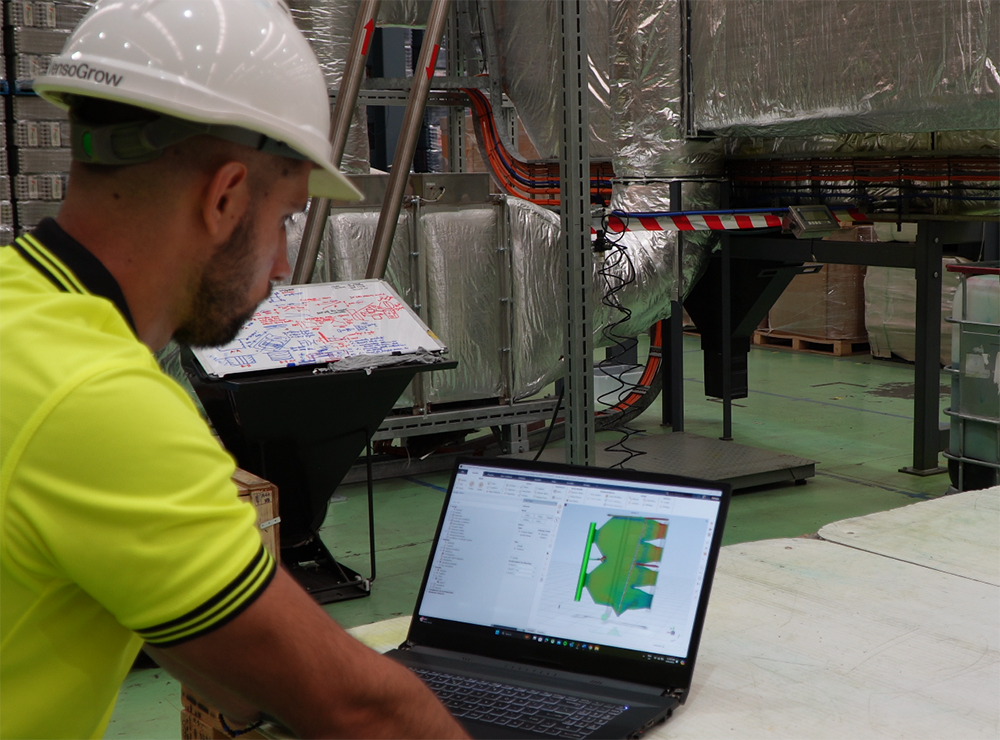
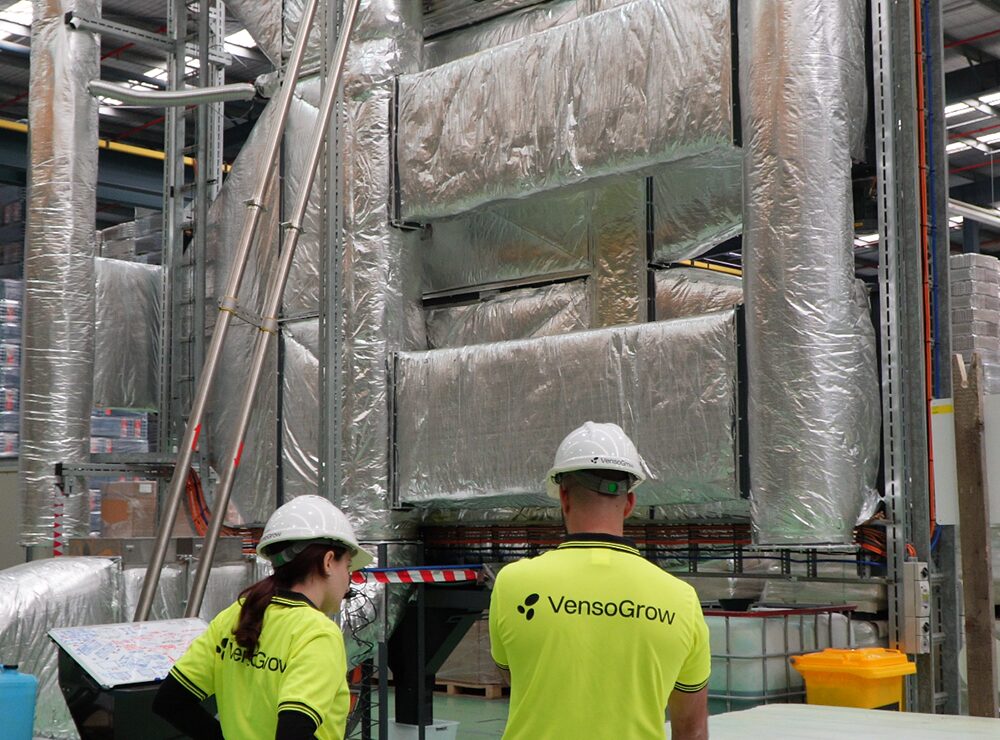
VensoLabs are currently commissioning and testing the seed coating prototype ready for demonstration to technology partners and potential customers. Their engineering team is also working on business cases for other notable industrial use cases such as reducing fossil fuels in concrete production, noxious gas scrubbing and solving major problems for coffee roasters such as high energy costs, uneven roasting and inefficient quenching issues.
Bringing Simulation in-house
In partnership with LEAP Australia, Venso Labs joined the Ansys Startup Program in 2021. “We joined the Ansys Startup Program to assist with a deeper understanding of our process technology and we were thrilled to be accepted as we could not otherwise afford the total costs of commercial software and training at that time. This programme has been a game changer for our team. Since then, our development engineer Marko has developed a very sophisticated CFD model of VENSOFLOW under the guidance of LEAP’s experienced team of engineers & scientists, particularly Adj. Prof David Fletcher and CFD/AI expert Lewis Clark. We successfully validated our CFD model with physical data from the 2021 pilot and augmented it with features such as the complex drying kinetics of particle coatings and impact on particle temperature, as well as examine particle feeding behaviour using Rocky DEM and Ansys OptiSlang to analyse key process optimisation parameters. In effect, this has replaced much of our time consuming and costly physical tests with virtual tests, helping us achieve our goals faster and smarter.”
Technical Challenges along the way
Marko describes the biggest technical challenges being “the time-consuming nature of the simulations, due to the many particles involved at any one time and the processing requirements to account for them. The way to work around this problem is to create simulations that sweep through a number of different variables which results in larger interpretation of the various physical phenomena. This takes careful thinking of how to create the geometry/domain and which variables are most sensitive. This technique helps to reduce the number of simulations needed to gather a larger interpretation. Utilising OptisLang can reduce the time taken to generate datasets which provide meta-modelling of the specified application.”
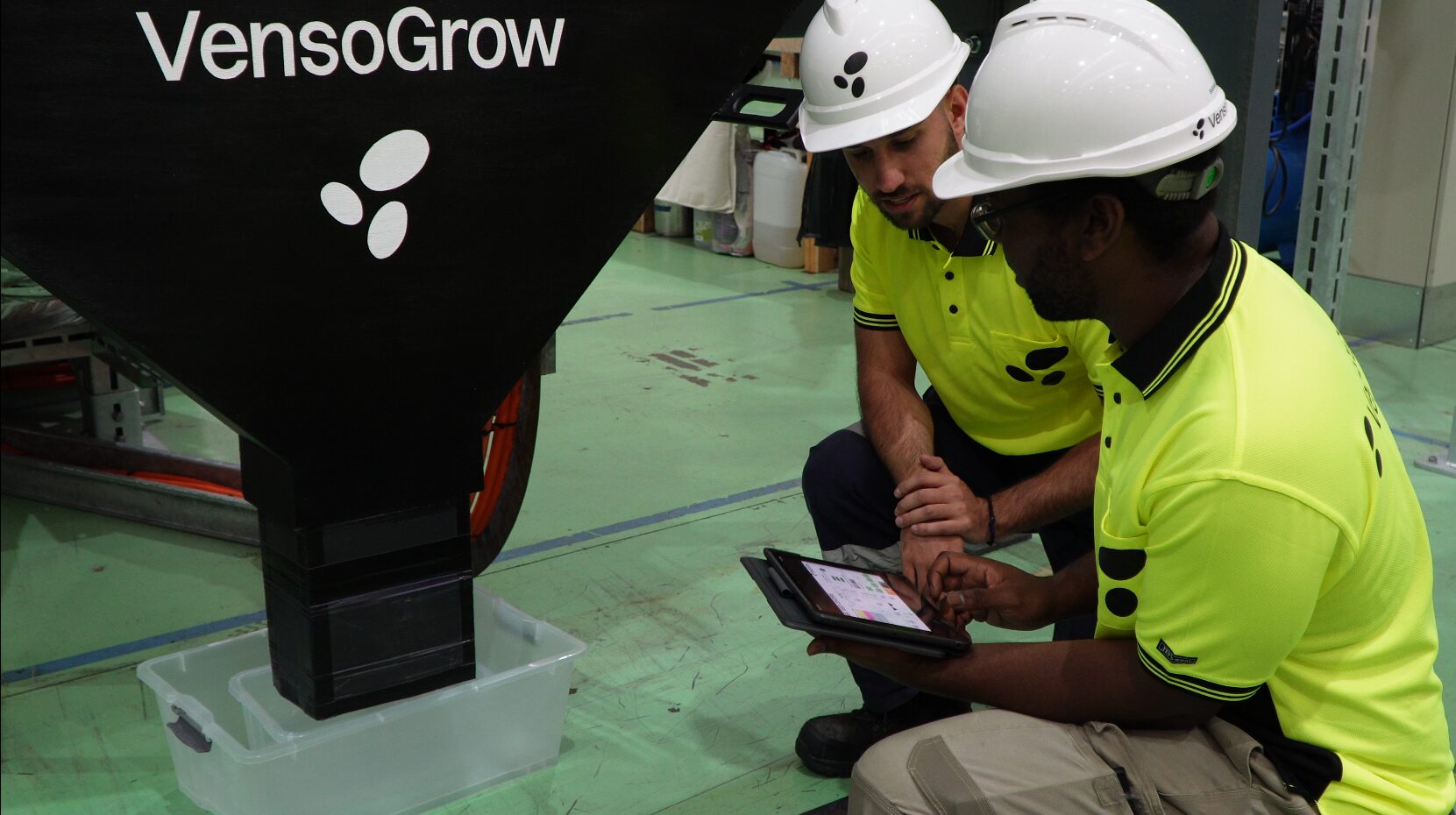
Another technical challenge has been “to interface specific models which are not contained in the original ANSYS Fluent user interface. We utilised Python code to add the 1-Dimensional Heat conduction equation coupled with transport phenomena involved in drying which we aim to place inside Fluent’s particle modelling considerations. Prof David Fletcher was instrumental in helping formulate the problem and code the relevant equations.”
“With CFD, we’ve greatly decreased the time taken to create experimental rigs for investigating inherent characteristics of the crossflow system. Our technical problems require careful consideration of variables relating to flow straightness and other flow phenomena that are not able to be seen directly with the eye, such as vortices in the gas flow and falling velocity values,” making it complicated and expensive to construct equipment to properly investigate these considerations that have been easily addressed with simulation.
Comparisons to Physical Testing at pilot and production scale
“In fact, we were employing some of that kind of physical equipment at significant cost, such as high-speed video, when analysing the results of the first pilot plant,” Caecilia expands. “CFD gives us the opportunity to investigate these phenomena within the scale of hours and days rather than months and years.”
Certain variables that are critical to an understanding of the VensoFlow process, such as the residence time and distribution of particles, can be very difficult and expensive to quantify experimentally. Caecilia confirms that “the VensoLabs C1 pilot took approximately 2½ years to design, construct and test. The rig was designed as a proof-of-concept trial of a completely novel process which means it took much longer to design and construct than a similar one now.” With the use of simulation, engineers can quantify these variables at a much lower cost, without the need to build a specific pilot plant rig for each concept.
Visual Insights into fluidisation behaviour
CFD has provided VensoLabs with an unprecedented visualisation tool to help document and communicate the behaviour of the gas/particle flow. Marko adds “we can visualise behaviour that had been a theoretical concept but invisible to us previously (before utilising CFD), as well as quantifying important parameters such as particle residence time – which otherwise requires expensive high speed video analysis at much lower resolution.”
One important design consideration which was informed by CFD simulation results is the “careful control of the gas flows to certain amounts of particles, which greatly effects the optimisation of our contactor. We have made a range of specific design improvements for future designs based on the data we have derived from Fluent and Optislang. Another design change/discovery found with the help of CFD was the ability to optimise the slip velocity on the particles with the same bulk flows, which results in an almost linear improvement in the heat and/or mass transfer between the particles and the gas. This discovery could not have been quantified in any other way than using CFD!”
Furthermore, Caecilia and Marko confirmed that CFD results were the basis for the data extraction and identification for the company being able to patent a new idea in crossflow (named VensoFlow). “The data on which the patent was formulated involved rigorous simulations with the help of both Ansys Fluent and Ansys OptisLang and confirmed the main differentiating feature of the new patent to our first patent family.”
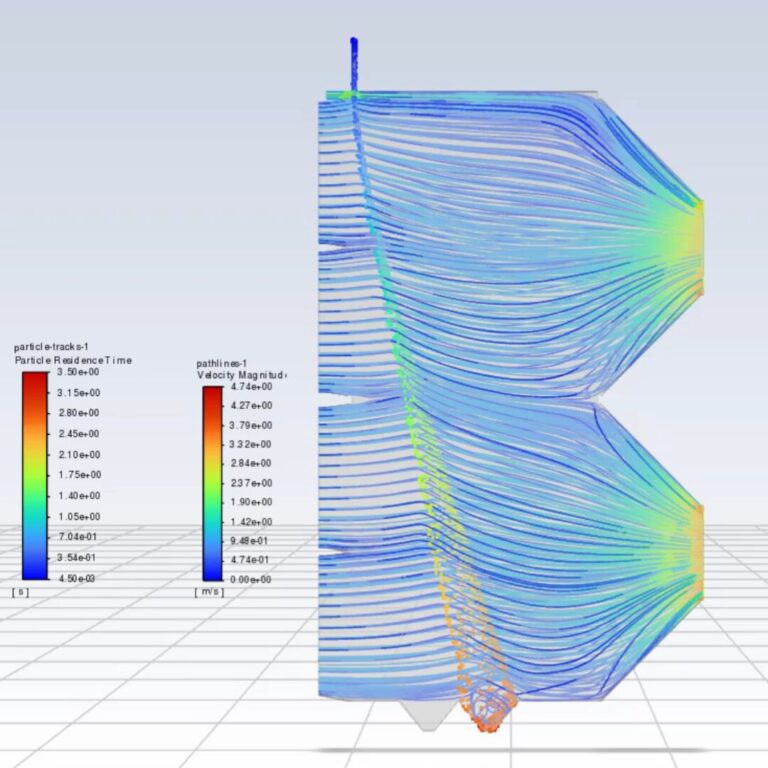
Figure 1. Typical simulation visually showing the impact of the gas flow caused by the falling curtain of particles
CFD has given Venso Labs great insight into the specific design features of crossflow that are not visible in experimental circumstances. Due to the great manipulability of the crossflow technology, CFD provides a very powerful “virtual testing facility” for investigating hypotheses about the inherent features of the technology and design alternatives.
As both CEO and custodian of her father’s legacy, Caecilia also values the ability of simulations to help build a deeper intuition for the physical phenomena occurring within the VensoFlow process, for both highly experienced and newer engineers alike. This expands to “the wider Venso Labs team and potential partners, who are able to see visual information within the defined domains of the simulation, such as flow velocity, particle temperatures and residence times. The graphical abilities of CFD allow for a vast array of videos, images and instant screen captures that provide an excellent communication tool, to convey the physical characteristics of the simulations as a basis for discussions with the tech team, lay people and potential partners and investors.”
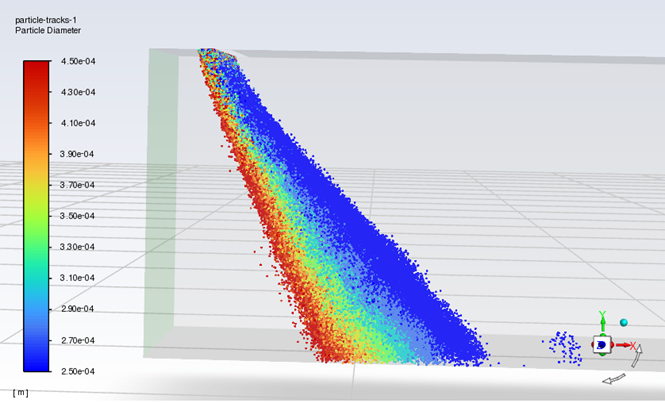
Figure 2. Typical simulation visually showing the spread of the different sized particles within the curtain
The Journey of a Startup
Support from government grants during the formative years of a startup can often be the difference between success or failure. Caecilia agrees that “learnings and images from our simulation work became instrumental in supporting our successful AusIndustry grant application. At that time, we provided graphical and numerical data output such as penetration of heat into a seed in the business case for the successful grant. We have since completed the AusIndustry grant and proven all of the USPs that we set out to complete, including getting industry-level coatings on different seeds and confirming superior microbial survival through the drying process.”
“We’ve also utilised CFD results in communications with potential partners and investors, and (lastly but not least) in helping substantiate our new patent claims.” Subsequently, obtaining government support to help VensoLabs to build their first commercial pilot has enabled them to demonstrate viable commercial applications to potential partners.”
What does the future hold for VensoFlow?
VensoLabs is currently engaged with chemical companies and seed business in testing their formulations using VensoFlow, and are currently working on another patent which aims to encapsulate the spray-seed interaction and wastage.
In the immediate future, Caecilia and Marko confirm that “Ansys simulations will continue to allow direct comparisons between existing gas-particle applications in terms of operability and cost benefit (CAPEX and OPEX) by conducting sensitivity analyses based on the size of the crossflow contactor and certain process requirements – our ‘sizing study’. For existing designs and experimental rigs that we develop, we will be able to optimise the performance by modelling different process variables – our ‘optimising study’.
Important for the strategic future of the company, Caecilia explains that “we will also use simulation in be development of newer patents under the umbrella of our VensoFlow technology, which typically need data to be quantified in such a way that may be difficult to obtain experimentally. We aim to use CFD as a tool within the Internet of Things interface for our process control systems designed for particular applications. By doing so, the CFD simulations can produce a Reduced-Order-Model (ROM) which can inform the setpoints within the system and allow a feedback loop of experimental results back to CFD for process optimisation.”
Ultimately, VensoLabs plan to develop a CFD-based app that allows potential clients to place their process or sizing requirements, for which simulations will run automatically.
Support from LEAP and the Ansys Startup Program
In talking with Caecilia and her team, she expresses her enthusiasm for the program and “cannot overstate how vital this programme has been for our startup! Commercialising deep tech is a challenging and expensive task and we are currently a small family business with a big vision – to help engineer’s solve the big problems, leaving people and the planet better off for generations to come. We would not be where we are today without ANYS Global software and LEAP’s Australia’s support.”
“The expert technical assistance from LEAP, including Professor David Fletcher and Lewis Clark, has been invaluable. They have provided our design engineers with highly skilled advice and support to build the model in an efficient manner and explore some interesting engineering and complex mathematics ideas within the CFD context, including the use of AI to speed up our understanding and investigations. This includes extensive investigations creating datasets supporting our Patent Family 2 claims.”
“The ANSYS startup program turbo-charged our R&D program to support this crucial first project, providing access to highly sophisticated modelling and sensitivity analysis software along with support from world class experts. Without that support, we would have needed to raise capital externally before having delivered a proven commercial process – difficult to say the least! Now we can focus on delivering a big win for our company, our partners, future customers and the planet. Our seed coating contactor will help improve crop yields whilst decreasing soil pollution and deliver enhanced sustainability and profitability for users. It will help us to meet the challenge of feeding 10B people globally. As we also explore other applications such as reductions in fossil fuels in concrete production, the impact we can have motivates and inspires the whole team. “
Caecilia Potter, Founder & CEO, Venso Labs
If you’re interesting to learn more about this exciting fluidisation technology and explore other potential industrial applications, you can find out more about VensoLabs and the VensoFlow process at their website.