Guest Post by Prof. Pier Marzocca, Associate Dean of Engineering (Aerospace Engineering and Aviation), RMIT University and Michael Scott, PhD Student, RMIT University, Australia.
In the School of Engineering at RMIT University, we are working with the Defence Science & Technology Group and the Royal Australian Air Force (RAAF) to conduct research on the use of emerging digital technologies such as Digital Twin, physics-based simulations and Augmented Reality (AR) tools to support NexGen aircraft sustainment. A retired PC-9/A aircraft, located at RMIT University, now serves as a research testbed, which can be seen in the video showing examples of Augmented Reality (AR) experiences developed by RMIT researchers and LEAP Australia. This cutting-edge project aims to further our learning and teaching strategies and provides a platform for our research undertaken at RMIT in collaboration with our partners in industry and defence.
We have been working with defence since 2015 on the development of new tools to enable them to enhance the sustainment of various aircraft platforms. Fortunately, the PC-9/A is a great starting point as it is an aircraft for which we have a wealth of knowledge. The available data supports the development of air platforms diagnostics and prognostics, predictive maintenance tools, including the one used for condition-based maintenance, all of which is essential for the next generation of aircraft sustainment.
In collaboration with LEAP Australia, we aim to blend the knowledge of these new technologies from industry with deep knowledge of the requirements from defence, to develop AR experiences that can help both in a learning and teaching environment for our students, but also provide a solid platform for applied research by our research engineers and scientists relating to innovation in design, training and aircraft maintenance.
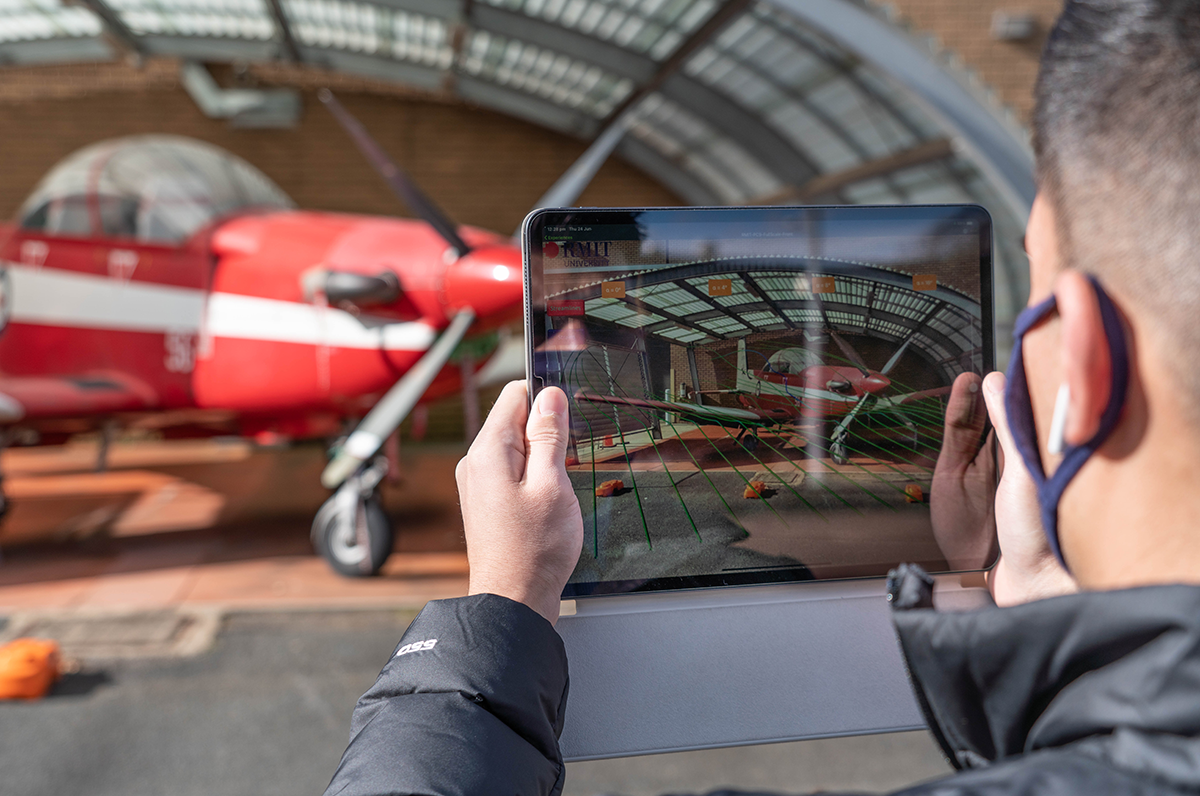
As an example, using Vuforia Studio, we have incorporated Ansys computational fluid dynamics (CFD) simulation results around the PC-9/A aircraft, which can be viewed by the use of either a HoloLens or an iPad. These results including digital content overlaid on the physical aircraft, such as streamlines for different angles of attack and three dimensional (3D) visualisations of turbulence intensity around the aircraft, all of which remain in place in 3D space as you walk around the aircraft and view the content from different perspectives.
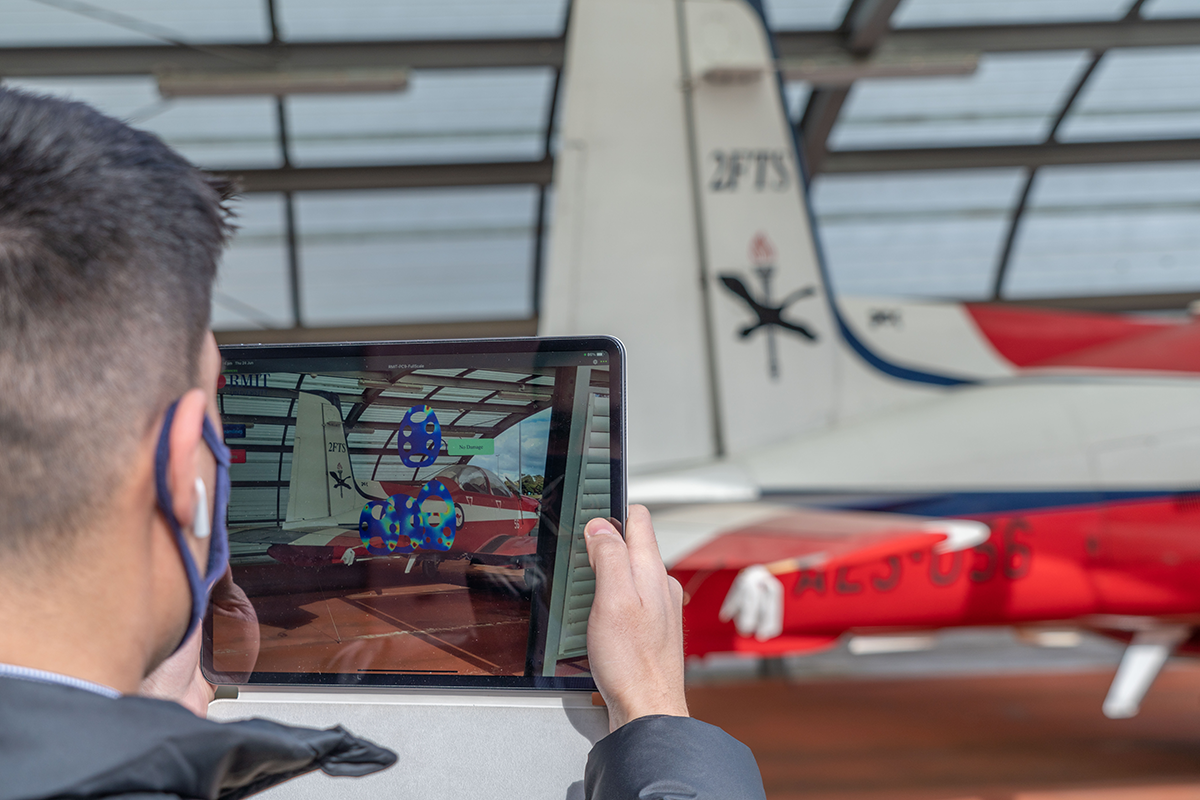
As shown in the video, albeit a representation for educational training purposes – we can also visualise finite element analysis (FEA) results showing deformation and stress/strain on different parts of the airframe that have been subjected to certain flight loads, providing students with an “X-Ray vision” like ability into the internals of the aircraft, as well as visualising stress results in full colour in 3D space. The FEA results show red hotspot locations where, based on certain flight loads and the number of flights, our model has identified potential areas that must be monitored for the initiation of cracks and fatigue failure. In future, this will provide maintenance engineers with an ability to locate potential damage following a flight or routine walkaround inspections and enable updated prognostics to assist with decision-making on whether the aircraft can remain in service or proactive maintenance can be planned ahead of time at the next scheduled check interval.
We believe this combination of physics-based tools, Digital Twin and AR technologies will increasingly be integral tools for both our teaching and research at RMIT. AR provides a near immersive and interactive way for our students to enhance their knowledge of the underlying physics. For example, they can better understand the airflow patterns during a particular aircraft manoeuvre and the subsequent loads on the airframe. AR provides the viewer with a greater spatial understanding of the physics-based simulation results applied to the physical aircraft at a true scale.
Based on this work, we also see great potential for fleet managers to use simulation-based digital twin data to increase their ability to identify potential issues on an aircraft, both for individual aircraft and at a fleet level. We anticipate they will be able to assess operational conditions for each aircraft and identify any aircraft requiring maintenance, which will reduce aircraft on ground (AOG) time, allowing maintenance events to be scheduled in advance. We are looking forward to supporting the RAAF and DSTG to further develop those technologies to a point that they will be used daily by aircraft operators.
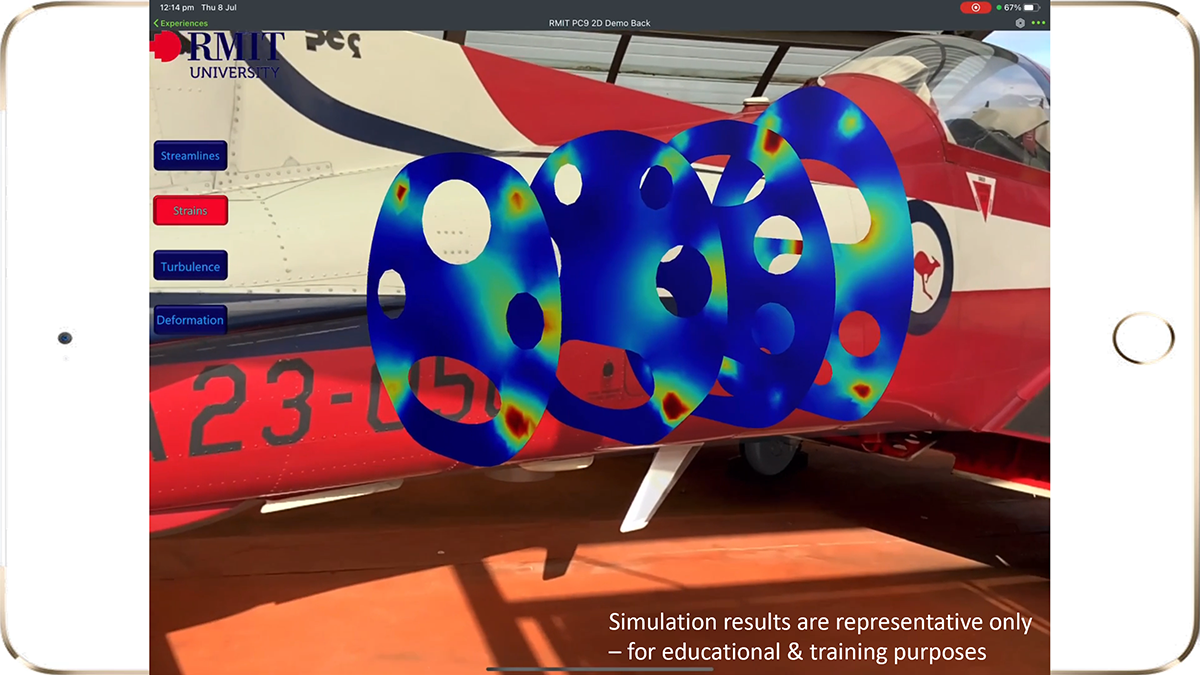
To learn more about the research or to get in contact with the team at RMIT and LEAP Australia, you may contact via:
- Professor Pier Marzocca, Associate Dean of Engineering (Aerospace Engineering and Aviation)
- Michael Scott, PhD Student, RMIT University
- David Graham & Imran Muthaliph at LEAP Australia