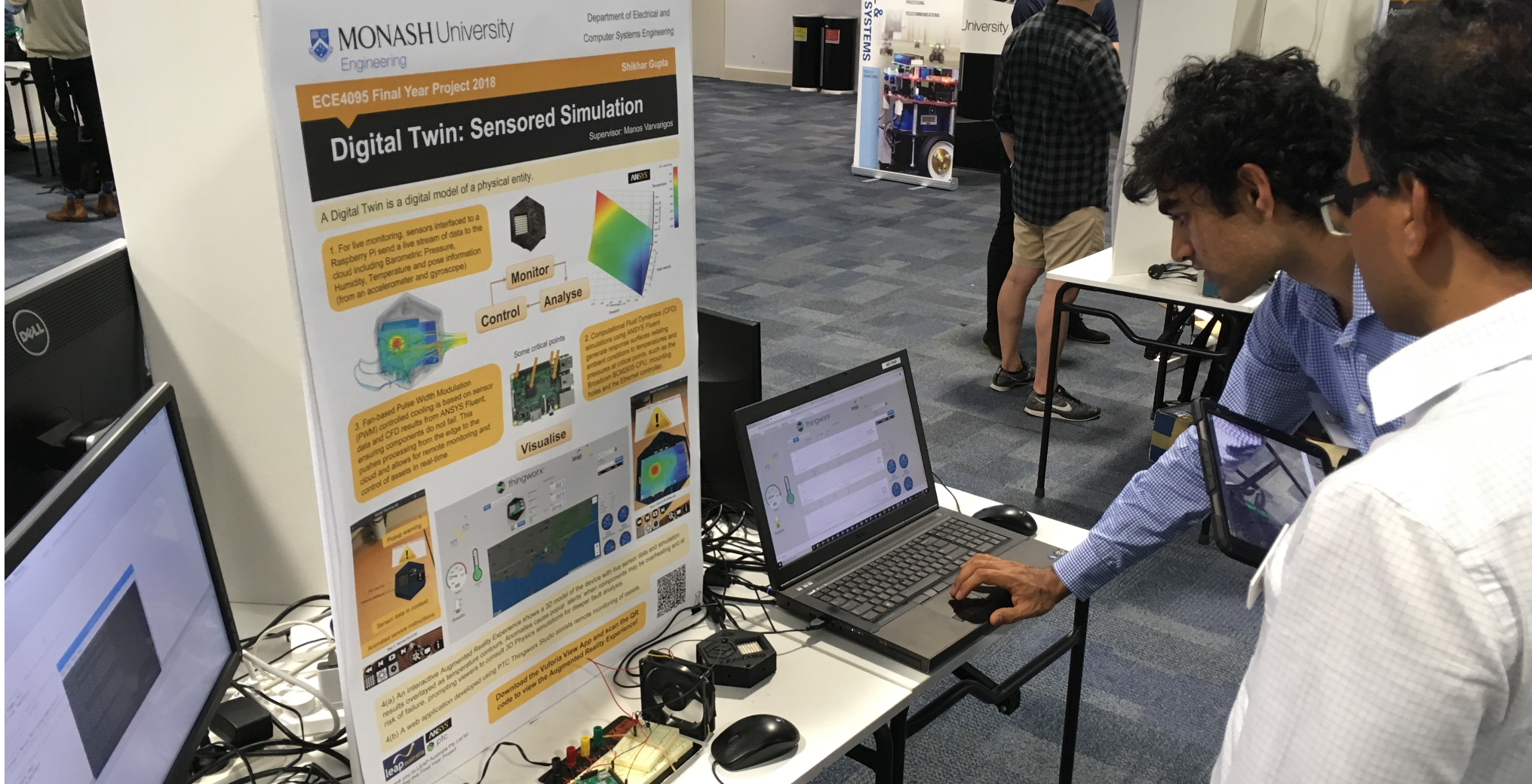
Guest Post by Shikhar Gupta, final-year student in the Faculty of Electrical and Computer Systems Engineering at Monash University, Victoria, Australia. Shikhar was a full-time intern at LEAP Australia over the summer of 2017/18, then completed his Final Year Project using LEAP & PTC software during 2018. The result of Shikhar’s work was presented last week at Monash University Spark Night where all ECSE final-year students showcase their final-year projects.
Setting out on this project, our aim was to create a working digital twin prototype that could be considered to represent a smart connected product operating out in the field. In doing so, I was able to demonstrate the process of connecting a product to the cloud, performing physics-based simulations to predict product behaviour under a range of conditions (in this case, using CFD simulations to inform fan cooling scenarios) and developing an IoT dashboard and AR experience to help monitor and service the ‘smart connected product’. This project has brought together key software technologies from PTC and ANSYS (IoT, AR, CAD, Simulation) that are available for students to use within Monash University with technical support & guidance provided locally by LEAP Australia.
This ‘digital twin’ of a representative smart, connect product showcases how sensor data can be readily interfaced via the cloud to allow managers to view the performance of their remote assets, in real-time. LEAP Australia has many clients across a diverse array of industries who would benefit from adding sensors to their remote devices, with data communicated via a ThingWorx server in the cloud and a web dashboard allowing remote monitoring & control of remote devices, including time-series charts, alerts and graphs and data analytics.
So how did my ‘smart connected product’ actually work? Sensor data such as barometric pressure, temperature and acceleration is wirelessly sent to the cloud via a Raspberry Pi. A separate Raspberry Pi reads that sensor data from the cloud and performs controlled cooling of a device using Pulse Width Modulation to control fan speed. The sensing and control response each rely on communication with a ThingWorx server, to push processing from the edge to the cloud. An ANSYS CFD Conjugate Heat Transfer model provides insights into the thermal performance of the board, beyond what sensors can provide in isolation (essentially providing you with an infinite range of ‘virtual sensors’ across the device, and also allowing you to predict cooling rates and performance under extreme scenarios).
A web dashboard created using PTC’s ThingWorx allows monitoring of multiple devices deployed across various locations – giving insight into the ‘digital twin’ of each device. An Augmented Reality experience developed using PTC’s Vuforia Studio allows you to convey the most critical information to technicians in the field, such as live sensor data visualised on each physical device, as well as specific service instructions. Popup warnings can alert the technician in the case of any faults, and overlayed temperature contours from the CFD simulations can be overlayed on the device via AR.
Personally, I found creating a web dashboard and AR experience with PTC software to be extremely accessible and simple to use. The user interface of ThingWorx and Vuforia Studio allowed me to quickly implement the IoT connectivity without requiring any significant programming skills. The user interface was very intuitive and sensor data can be bound to elements in AR and ThingWorx IoT mashups through simple drag-and-drop functionality -this allowed me to focus on designing the dashboard rather than worrying about writing heavy Javascript code (although if you have those skills, you can do that too which opens opportunities for more advanced customisation if required).
Here is a video of my Digital Twin demonstration in operation at Monash University Spark Night – an opportunity for ECSE students to showcase their final-year projects:
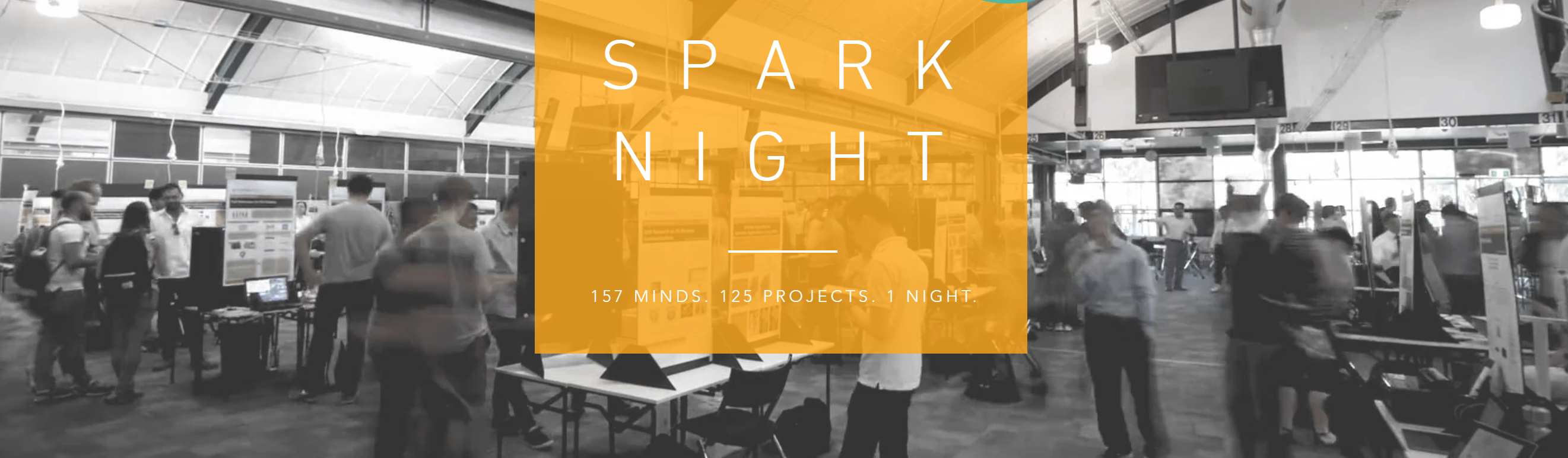
During my internship, I also found the staff at LEAP Australia to be extremely knowledgeable and supportive of my final-year project. I have learned an incredible amount from them and I would recommend any engineering student in a similar position to me, with an interest in the application of new technologies such as IoT/AR/Simulation to real-world engineering problems, to consider applying to work at LEAP or within their customer base in industry. I would also like to thank all of the staff at LEAP Australia for helping make this project possible.