Modern Systems require modern solutions
As the scale and complexity of today’s interconnected engineering systems grows, so too does the complexity of the engineering design process behind them. No longer do systems operate in isolation, unaware of the world or technology around them. Instead, devices are more connected than ever, transmitting and receiving data hundreds, if not thousands of times a second. In turn, systems act and respond, taking in vast amounts of data to decide on the best possible course of action.
For decades, the adoption of physics-based simulation has grown rapidly across all avenues of engineering and product design. CFD and FEA are arguably household acronyms within the engineering space now. However, the new systems of today require more wholistic solutions, and the ability to quickly and intuitively understand these complex systems, particularly in those “what if” scenarios where the system absolutely cannot fail.
Digital Mission Engineering
This brings us to the idea of Digital Mission Engineering (DME), and a Design Reference Mission (DRM). Traditionally, engineering processes tend to be segmented, operating in isolation from one another. This typically leads to drawn out project timelines, doubling up on work, and miscommunication between team members.
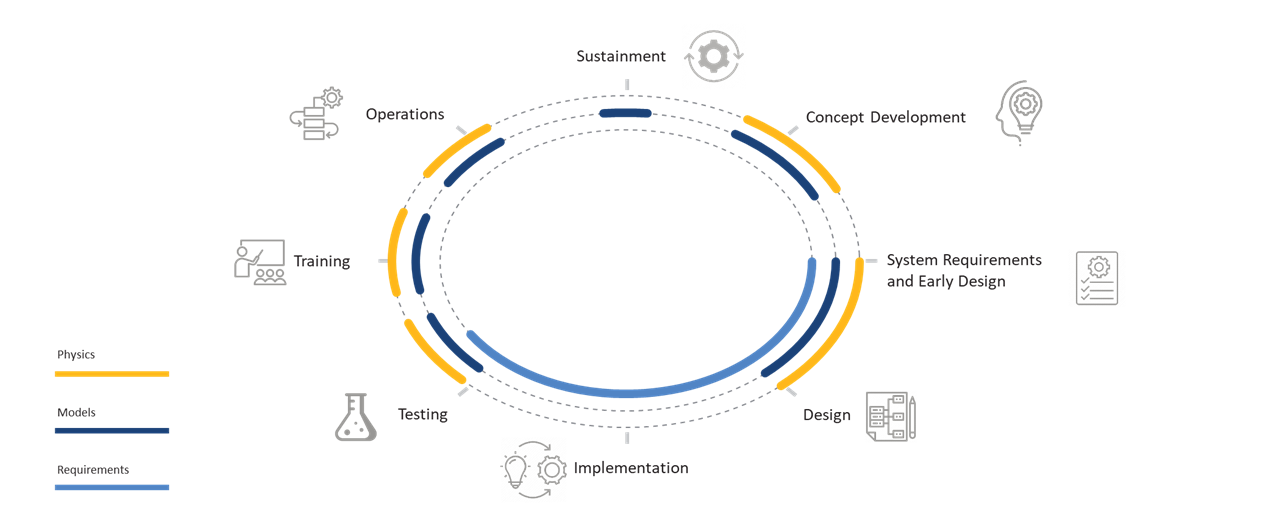
Figure 1: Visualisation of a traditional engineering and design process, often disjointed across various sections, team members and design tools
By comparison, the DME approach seeks to bring the entire engineering process into one continuous process through the use of digital modelling, simulation and analysis to incorporate the operational environment and evaluate mission outcomes at every phase of the lifecycle. Doing so allows for a single environment in which all elements of the system are assessed and evaluated as one interconnected system. In turn, any change to an upstream component, such as a sensor, will immediately reveal the downstream effect on the overall system and mission success. Moreover, components are no longer tested in isolation, but rather in an environment accurate to their real-world implementation, including crucial factors such as vehicle motion, atmospheric effects, radiation, terrain, etc.
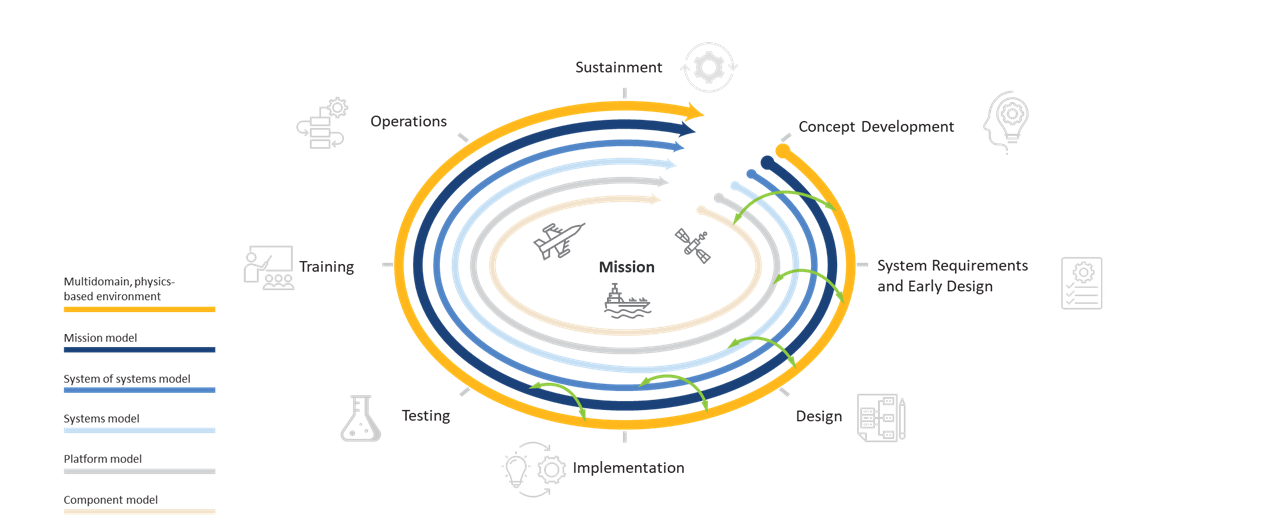
Figure 2: The engineering design process unified under a single multi-domain simulation environment, producing a cohesive design, testing and analysis environment across the entire project.
Design Reference Missions
By continuation a DRM is a representative mission profile that sufficiently describes the intended system use across its nominal and most stressful operating conditions. A well-constructed DRM will;
- Identify the operational environment
- Model interactions between system components
- Define operational situations and behaviours
- Establish measures of mission effectiveness
Crucially, a good DRM does not cast away the traditional CFD and FEA work an engineer might be familiar with, but rather it will integrate these results into the DRM to best describe the system and its performance. CFD aerodynamics, structural deformation and high-fidelity electromagnetics computations are all typical examples that serve to enhance the accuracy of a DRM and its ability to most accurately mimic its real-world performance.
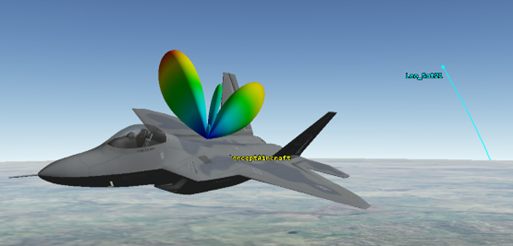
Ultimately, a DRM aims to unify the engineering process. Early concept development work can rapidly evaluate potential solutions and system configurations, design and testing can compare specific component choices and their respective performance, and finally, long-term lifecycle analysis can ensure the system remains fit for purpose throughout its entire intended lifespan.
How can we simulate a multi-domain DRM
For the bulk of this series, we will explore a number of DRMs built in Ansys System Tool Kit (STK). STK facilitates a physics accurate environment across air, land, sea and space domains, allowing us to combine various simulations assets to ultimately visualise, analyse and optimise our solutions to a given problem. It can be thought of a wholistic, multi-domain solution for all mission planning, solution designing and system test and evaluation work. In other words, an environment for the modelling and analysis of complex “systems of systems,” bringing together all the individual components, sensors and platforms to truly understand how these moving parts will function in their shared mission or goal.
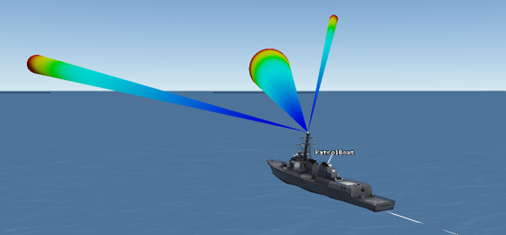
As we’ll see throughout this series, a DRM is not limited to one piece of software. In fact, bringing simulation models and results into STK from dedicated FEA, CFD and EMAG solvers can enhance the overall fidelity and realism of the DRM. Likewise, pairing STK with further model-based system engineering tools like Ansys Modelcenter can open avenues towards parametric study and design optimisation work.
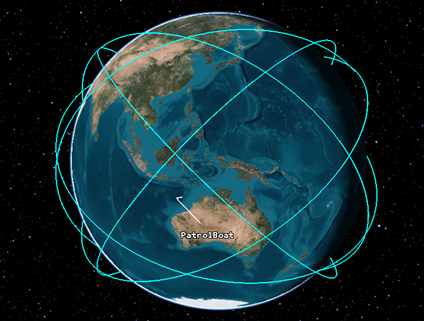
LEAP Australia DME Series
In this new series we’ll be exploring a variety of DME applications and industries. We’ll look at how DRMs can be used to enhance the traditional engineering process, and ultimately improve or ensure mission success across air, sea, land and space domains. Series by series we’ll examine applications from civil through to defence and beyond. Everything from telecommunications design in dynamic urban environments, to satellite constellation design for environmental emergencies, to hypersonic vehicle detection using EOIR sensors. Be sure to check the DME blog page for all things DME, including guest blogs from users about their in-industry use of the technology. Upcoming series topics include:
- Digital Mission Engineering: Enhancing Student Rocketry Launches (Coming Soon!)
- Digital Mission Engineering: Thermal Analysis for Antenna Deformation (Coming Soon!)
- Digital Mission Engineering: Urban Telecommunications with RF Channel Modeler (Coming Soon!)
If you have any questions about DME, physics simulation, and the role this technology could play in your particular application, please feel free to contact us here at LEAP Australia.