Guest blog by Jeremy Pryor, Monash HPR / Monash University
Monash HPR (High Powered Rocketry) is a student team from Monash University dedicated to the design, analysis and construction of high-powered rockets. Formed in conjunction with the Australian Universities Rocket Competition (AURC), Monash HPR designs and constructs rockets to compete in the 10,000 ft and 30,000 ft categories of AURC. In 2021 we also intend to compete in the Spaceport America Cup.
One of the most important, if not the most important, structural components of Monash HPR’s competition rockets is the motor bulkhead. Its role is to transfer the thrust from the motor to the airframe such that the entire rocket accelerates (not just the motor!). The loading on the motor is assumed to be purely from the maximum motor thrust with an additional scaling factor for safety.
In rocketry, the name of the game is to create the lightest possible components. We always attempt to make components lighter – without compromising safety. In the most recent design of the bulkhead, our student engineers at Monash HPR used Ansys Discovery Live to rapid prototype bulkhead designs using both parameter-driven optimisation and topology optimisation. We then utilised the Ansys Mechanical solver to validate that the stresses for each design were under a specified tolerance.
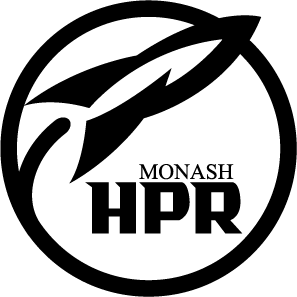
Season One: The MKI bulkhead created in season one of HPR (August 2018 – June 2019) was bonded to the airframe by epoxy under shear loading. This resulted in a large interfacial area leaving large amounts of material along the wall making the component heavy. The design of the bulkhead at that time was purely done by CAD – while FEA was run afterwards in Ansys to ensure safety, we did not yet use simulation to thoroughly analyse design iterations of the bulkhead. As such, the MKI bulkhead came in weighing 1.2kg and had a factor of safety of 10.
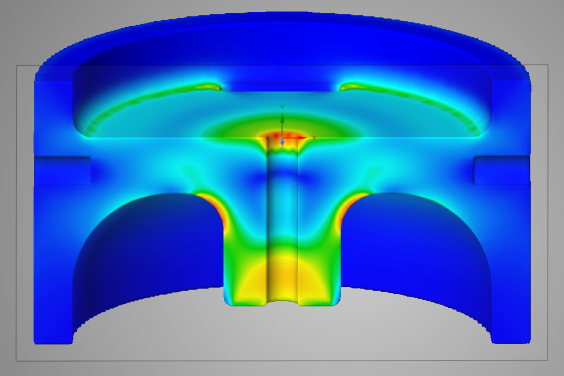
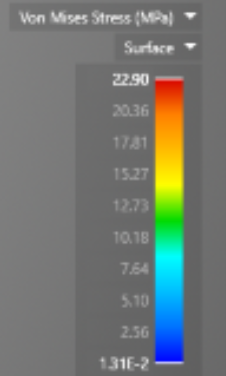
Season Two: Embarking on a new MKII bulkhead design for season two (June 2019 – Present), the team had a goal to design a new bulkhead that was significantly lighter than the previous iteration. To achieve this, we used an approach leveraging design revision, parameter-based optimisation and aggressive topology optimisation utilising the new technology in Ansys Discovery Live. Unlike MKI, the MKII bulkhead is constrained vertically by an inner tube leading to a support under compression, not shear, allowing the vertical interface and radial interface to be smaller relative to the MKI design. Comparing the S1 and S2 bulkheads:
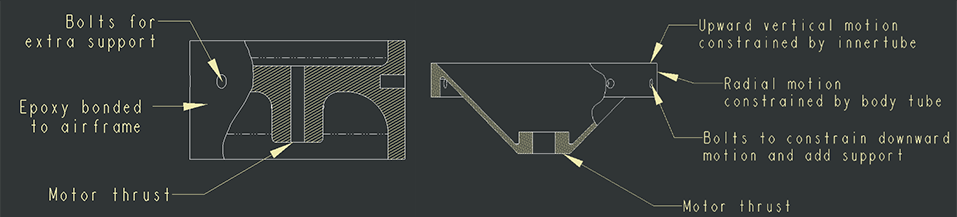
The bulkhead starts off as a billet of d100mm x 40mm, the boundary conditions are applied to imprints on the surface and the geometry. The bulkhead is then topology optimised to an 80% mass reduction. The results show that the maximum stress is 38MPA.
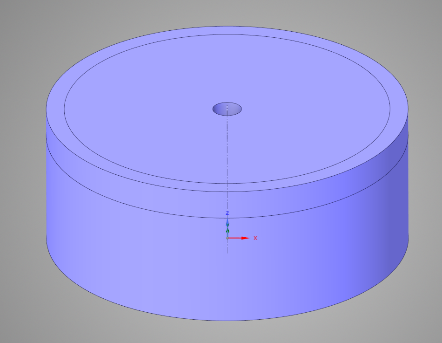
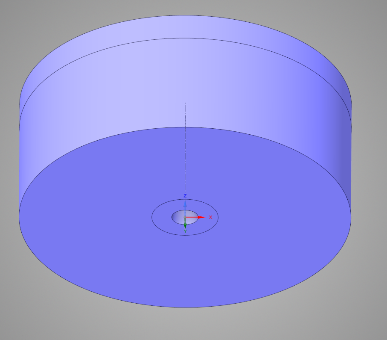
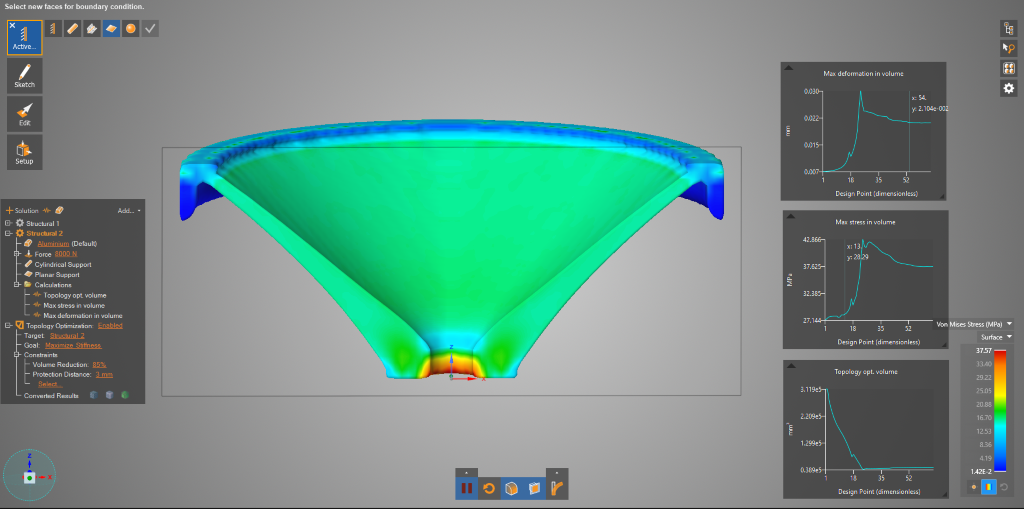
If the amount of material to be removed is increased to 92% then a 4 spoke design appears to evolve. Due to manufacturing constraints however, we decided to stick with an axisymmetric design that is easier to manufacture on the lathe (with no interrupted cuts) and concerns over its response to lateral loading which may be more unpredictable due to the loss of radial symmetry.
We were now able to create a CAD model of the optimised bulkhead which contained the system constraints i.e. introducing space for the parachute eyebolt. From there, a parameter-based optimisation on each geometrical feature could be performed such that the mass could be reduced, and the bulkhead would still fulfil the system requirements.
One such batch of parameter-based optimisations was varying the thickness of the arms and determining the maximum stress that develops:
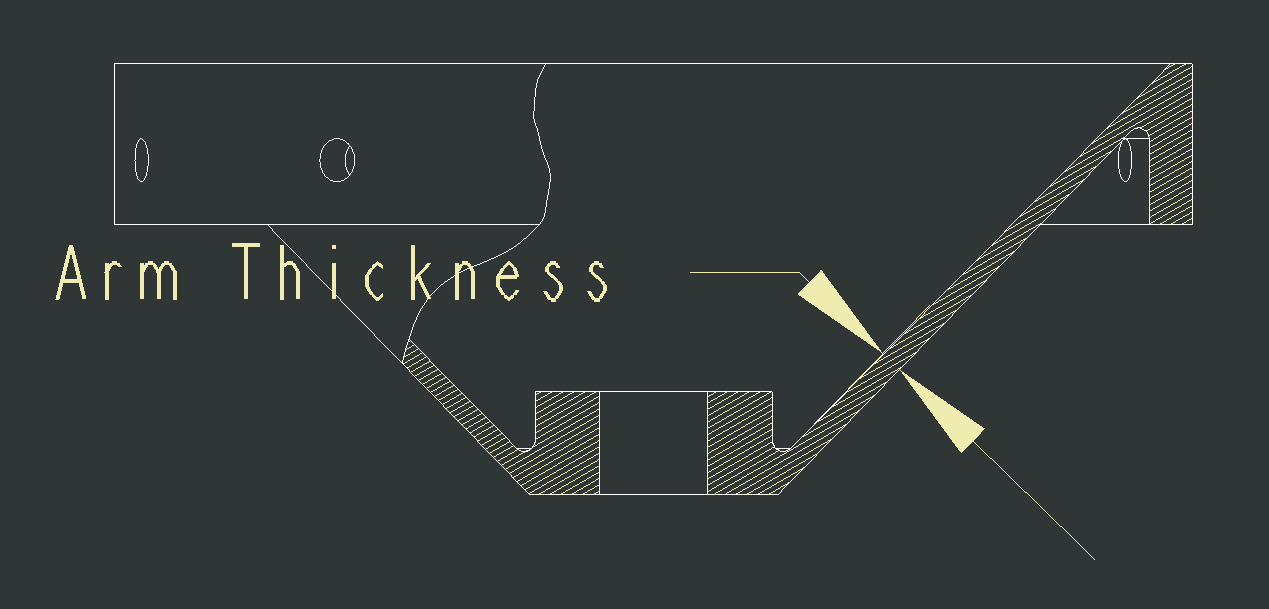
These results were captured using half fidelity Discovery Live simulations (noting that the yield stress of T6061-T6 aluminium is 240MPA):
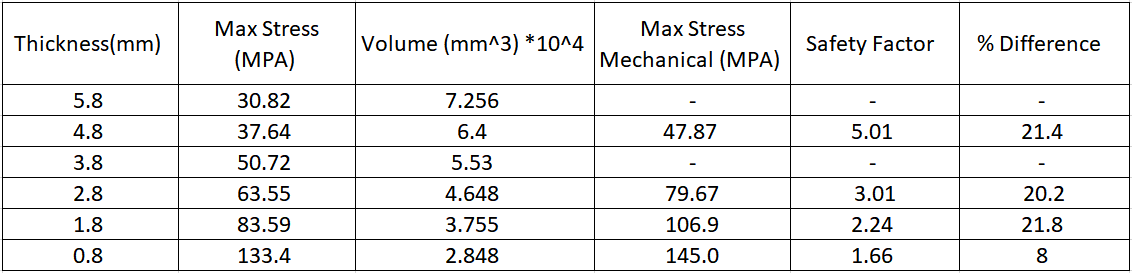
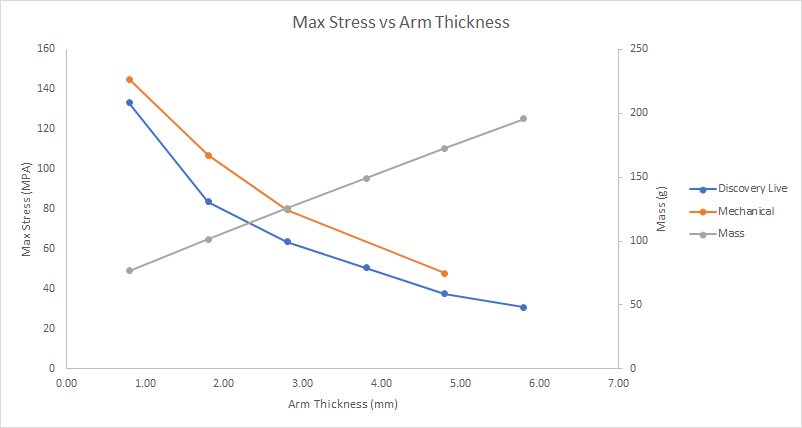
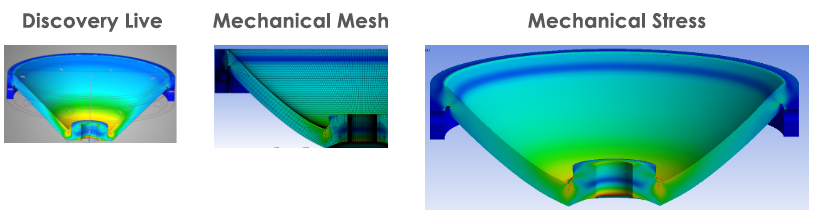
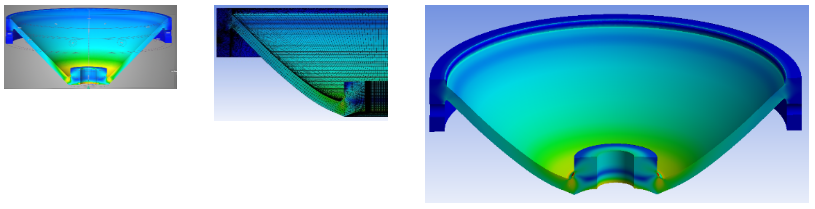
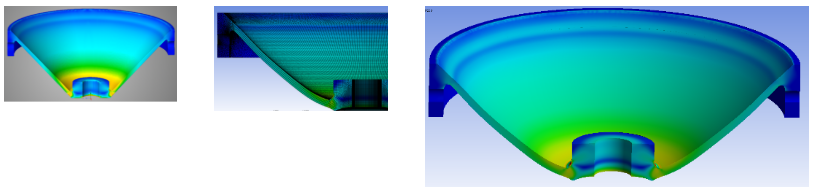
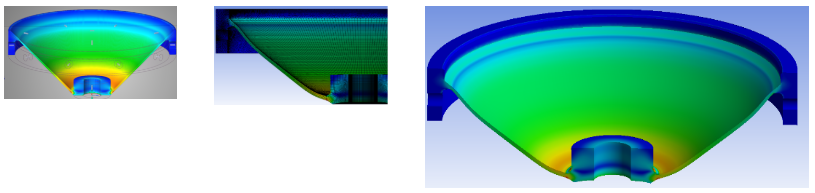
Using Ansys Discovery Live our student engineers could rapidly prototype different bulkhead designs in a very interactive way – comparing the stress distributions and weight of each bulkhead design iteration, allowing us to very quickly remove mass and find a very promising design candidate. One of the biggest benefits was working in the integrated Ansys SpaceClaim interface for geometry creation/modification (as well as the automatic meshing) which allowed us to see and interact with the simulation results much faster than running a typical FEA model. We found it particularly useful to use SpaceClaim to push faces in or out or add fillets – giving us immediate feedback on the effects of these change to the stress distributions and overall mass.
After validating our Discovery Live results using Ansys Mechanical, the team had extra confidence in the FEA results. After design reviews we decided to proceed with the arm thickness of 1.8mm in our final design. This gave us a safety factor of 2, a total mass of 101g and avoided the wrinkling as seen in the 0.8mm bulkhead arms – delivering the team a weight reduction of 85% while remaining within an appropriate factor of safety.
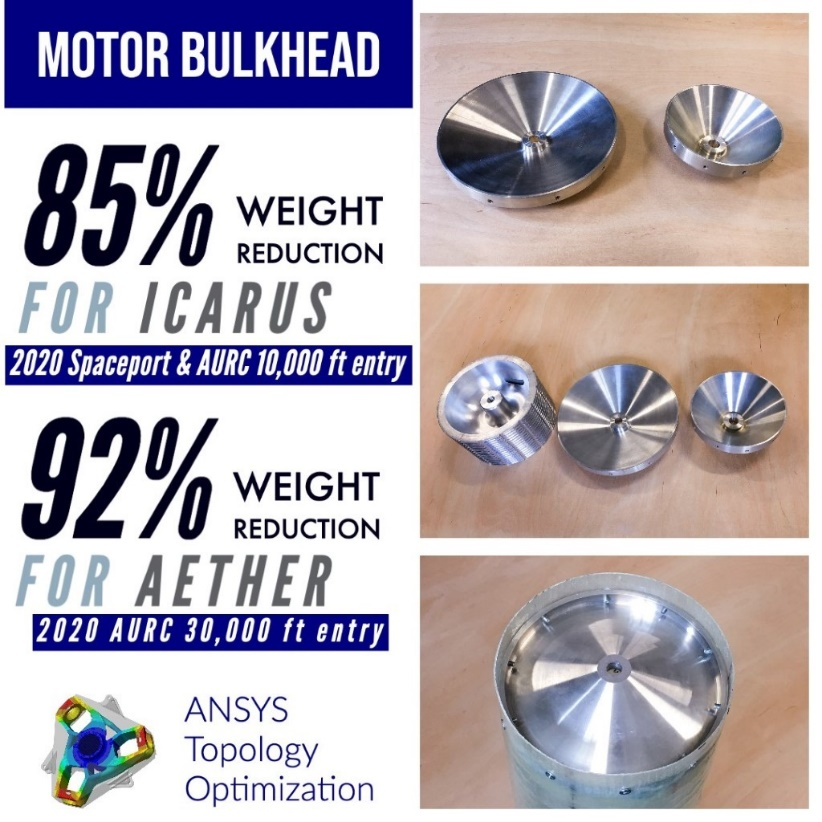
HPR also uses Ansys Fluent to determine the aerodynamic forces and moments acting on the rocket for use in flight path modelling using our custom build 6 degree of freedom solver SATURN and determining the aerodynamic loading on the structure. We also use Ansys HFSS to determine the antenna performance and the interference of the antenna on the flight hardware and the flight hardware on the antenna.
After a successful 2019 campaign at AURC, Monash HPR aims to have a student-researched and -designed hybrid rocket motor, capable of transporting payload to 10K feet, developed by early 2021. This project will include extensive use of flow and structural analysis using Ansys to gauge the performance and safety of the motor.
You can also view a video of a recent presentation by Monash HPR (at Converge 2019) which provides a good overview of the use of Ansys simulation within the team: