Guest blog by Joe Zadnik, Aerostructures Lead at Monash High Powered Rocketry (Monash HPR)
Monash HPR is a student team based at Monash University, founded in 2018 and now consisting of more than 100 members. Notably, we are a multidisciplinary team with students from faculties all across the University – Design, IT, Commerce, Arts, Science, and of course, Engineering.
Each member plays their role across a range of projects – all falling under our overarching vision to:
"become a well-renowned contributor to the development of the Australian space industry on the foundations of innovation and professionalism, using our platform to influence passion for rocketry in younger generations."
Our team heavily utilises Creo 3D CAD and Windchill PLM for our product development work, including internal research and development projects. One of our largest research projects is designing and developing our in-house hybrid motor ‘Solaris’ which will ultimately allow us to greatly reduce our cost-per-launch when compared to commercial off-the-shelf rocket engines ($50 compared to $600).
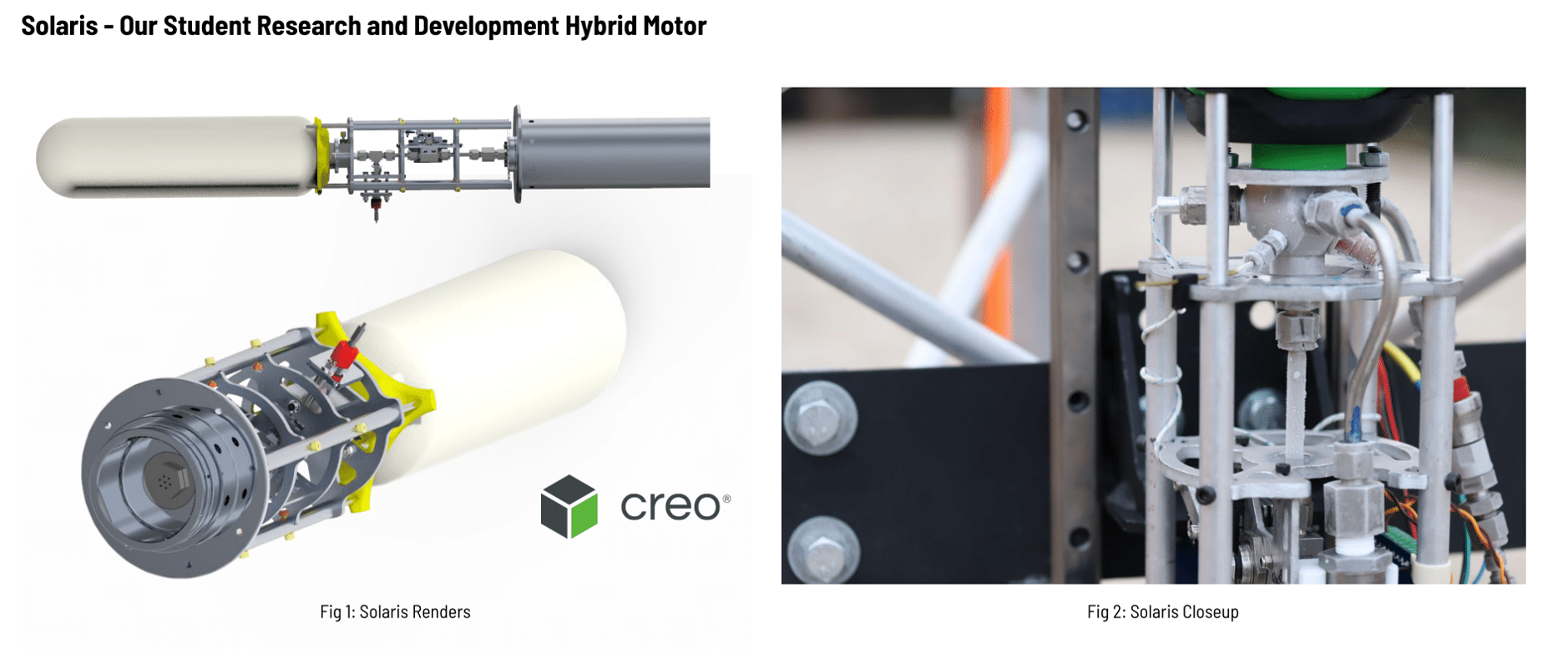
Creo has allowed the team to create 3D renders of Solaris, consisting of many complex parts and systems. Handling the oxidizer within this system is quite a complex process, requiring a significant amount of valves and piping. Creo allows us to develop and integrate all these complex CAD parts into the final assemblies using various CAD produced by third-party manufacturers and assembling it all in the virtual world, helping us do our final checks and making sure that the design was robust.
The team recently performed some hot fire testing of Solaris which proved that we have a working design as you can see in this video:
The main aim of our research projects is to have prolonged timelines to develop components for our competition entry rockets. This includes the Australian Universities Rocketry Competition (AURC) along with the Spaceport America Cup, of which we recently returned from in June with our entrant Project Aether.
At the 2022 Spaceport America Cup, the team launched internationally for the first time and brought home some results we are incredibly proud of. We achieved an apogee of 28,439 ft AGL, with our in-house trajectory simulator, SATURN, predicting this apogee to within 1.5%. Monash HPR placed 6th in our category and 2nd in the Charles Hoult Award for Modelling & Simulation. Additionally, the team was selected to present to all the teams and competition officials on a podium session called: “Small design changes with a disproportionate effect on trajectory”.
As an engineering team we are heavily dependent on technology to support us in our work.
Development of Project Aether started with an “OpenRocket” concept. OpenRocket is an open-source tool which is great for quickly estimating the parameters of a rocket design, but the design features available in OpenRocket are severely limited. We use PTC Creo, supported by the team at LEAP Australia, to take all of our initial concepts, sketches and designs and turn them into a detailed 3D concept model. We find Creo’s interface easy to use and this is especially valuable when we have such a diverse team of students (with various backgrounds and prior experience), allowing everyone to easily learn and contribute.
Creo allows us to create assemblies consisting of both simple geometries, like airframe tubes, as well as relatively complex geometries that are required to optimise our airframe (such as revolves for the unique geometry of our nosecone, or our transition which require parametric design).
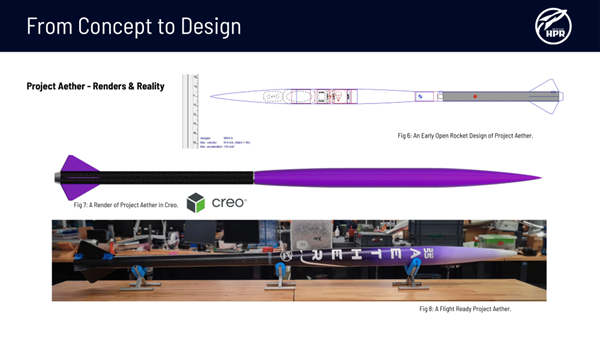
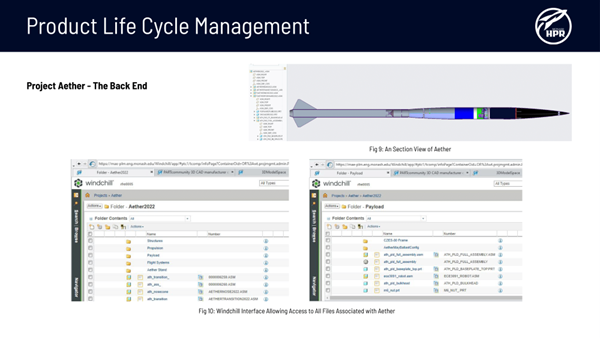
One of the features we are most grateful for is the seamless integration of PTC Windchill with Creo. Windchill allows us to catalogue all of our many parts and helps us work together by neatly organising files into our pre-defined cataloguing system, so team members can access any component they need across the entire rocket (helping to understand how it interacts with the overall system). Windchill also allows easy and effective management of the permissions for editing/viewing within our active CAD assembly, which helps the team to function while multiple individuals are working concurrently on the numerous parts that make up a rocket (and ultimately bringing them together into a final assembly).
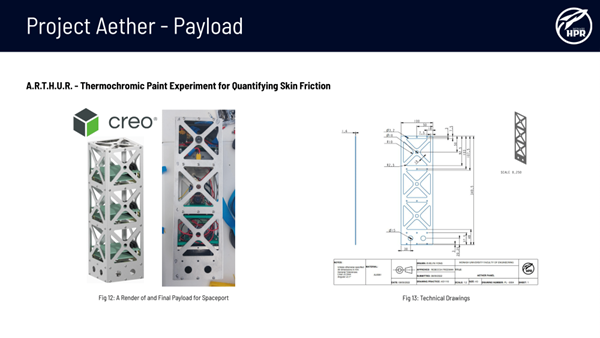
This year, our payload featured a thermochromic paint to investigate the skin friction and surface heating of our rocket. The competition payload is defined by a standard CubeSat format – meaning that it was able to be designed in place and iterated upon, while the rest of the rocket developed around it.
Furthermore, we are able to use Creo to transform our parts into technical drawings that follow AS1100 standards. We require these to fulfil competition expectations, as well as to enable us to outsource some of our manufacturing.
Finally, LEAP Australia also provides us with access and mentoring for the Ansys Multiphysics simulation suite. It is important to the team that all components that are implemented on the rocket are thoroughly tested using virtual simulations to prove their suitability for their use cases. The team has used both topology optimisation and FEA on numerous components, such as on Aether’s bulkhead shown below to minimise mass while ensuring an appropriate factor of safety.
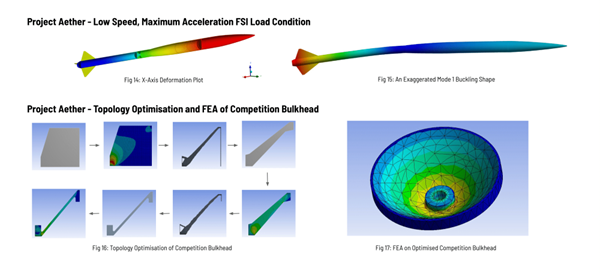
We simulated Fluid-Structure Interaction (FSI) on our airframe, checking both the max q conditions and also checking the low speed, high acceleration case – as shown in the figure above. Our dynamics team also performs an immense amount of CFD to both optimise rocket performance and feed aerodynamic derivatives into our trajectory simulator.
This blog post has been a really quick insight into a multi-year development project, which has been enabled by Creo and Windchill, and we are super excited to share these details during the Creo 9 launch recently in Melbourne. You can find out more about the Monash HPR team at our website. You can also watch the full recording of our presentation at the Creo 9.0 launch in Melbourne in this video: