Since the early 1940s, technological developments in Printed Circuit Boards (PCBs) have been a key driver of improvements across the electronics industry, in the process transforming almost every aspect of our everyday lives: from devices in our homes and workplaces, to the ways that we both commute and communicate.
Macro trends in the electronics industry such as Industry 4.0, the Internet of Things (IoT), drones, smart home technology and autonomous vehicles are continuing to push PCB technology to its limits. Electronics engineers are now needing to focus on more than just the electromagnetics aspects of PCB design, and are increasingly concerned with the need to continually lower power consumption as well as thermal and vibration issues linked to reliability concerns in harsh environments. Many recent high-profile electronics failures have caused the loss of connectivity, control, data and have even had the potential to endanger human lives (as anyone who tried to carry a Samsung Note 7 on-board a flight in October 2016 can attest!). This in turn has cost the industry tremendous amounts of money and caused untold damage to the reputation of some key brands.
In Australia, local electronic manufacturers are typically SMEs, often with a small team of just 5 – 50 staff who work on thematically diverse and challenging PCB projects. These PCB projects are often just part of an entire turnkey solution, from design work through to the delivery of a finished product. Also, these local companies are often targeting sectors such as Defence, Mining and Outdoor which require ruggedized products that typically need to survive harsh and extreme conditions. In such cases, to deliver a successful product it is more important than ever for PCB designers to consider the full lifecycle aspects of their PCBs: beginning with the soldering process in manufacturing, through to assessment of fatigue after many years of operation.
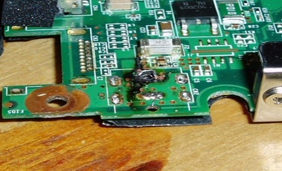
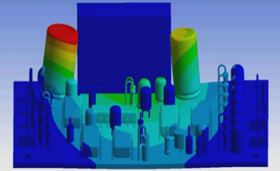
© expertfea.com
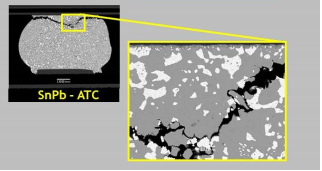
© Alcatel Lucent, Intel, Sanmina
To properly address these design challenges, successful electronics developers are designing PCBs with thorough consideration of all Multiphysics aspects. A complete Digital Prototype of your PCB is undoubtedly the most efficient way to assess PCB performance as early as possible in the overall design process. But only a comprehensive virtual PCB testing platform will be able to cost effectively and efficiently address all engineering issues: from EMI/EMC to Vibration and thermomechanical reliability.
In the following series of blogs, LEAP Australia will present an overview of the ANSYS Workbench Platform and how it addresses common design and reliability challenges in electronics development and manufacturing.
Please stay tuned for each of the posts in this series, covering topics such as:
- DC Drop Analysis
- Dynamic Power Integrity (PI)
- Vibration Analysis
- Thermal-Structural Fatigue Analysis
- Signal Integrity
- EMI/EMC Analysis
In the meantime, for more information or to arrange a call with one of LEAP’s electronics experts, visit our website to learn more about Electronics/Electromagnetics simulation.