Digital Twin
Engineering design and simulation software has traditionally been used for new product design, but with the advent of advanced embedded sensors, engineers can now use this data to create digital twins. Digital twins can be used in real-time systems analysis to schedule predictive maintenance and implement performance optimisations
When a product is IoT enabled the data collected from its performance in the real world can be tracked in real time and fed back into digital modelling tools to create a digital twin. The digital twin is then used to monitor performance and operating conditions to identify problems as or even before they arise and investigate and implement solutions on the fly. By displaying live data from the operational product, the digital twin provides unprecedented insight into what is happening ‘under the hood’, visualising any measurable data sources in real time.
LEAP Australia is proud to partner with PTC and Ansys who are at the forefront of digital twin technology; bringing together traditional manufacturing and design tools such as computer modelling, data management and simulation and connecting them through the Internet of Things to enable true end-to-end product lifecycle management. Digital twins created using Ansys simulation tools optimise the operation of devices or systems, save money by reducing unplanned downtime and enable engineers to test solutions virtually before doing physical repairs.
PTC’s market leading IoT platform ThingWorx powers the data connectivity of the digital twin and allows for easy, low-code creation of meaningful data dashboards to help users understand their designs.
Check out the video below demonstrating how Flowserve have implemented the digital twin to better understand and improve their pump designs.
Want to learn more about Ansys simulation solutions?
Complete the form and one of the experts from our Ansys team will contact you to discuss your needs.
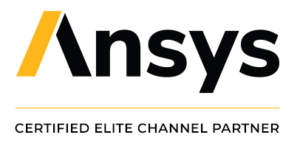